weo
Basic Member
- Joined
- Sep 21, 2014
- Messages
- 3,012
Hello all. I hope everyone continues to keep themselves and others healthy and safe.
I noticed my TC is starting to wear out, and am planning on ordering a couple to have on back-up.
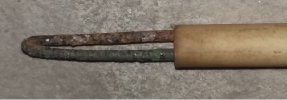
1) Is it possible to cut the corroded portion off, and if there's enough left, bend the remaining portion into a U and use? I don't think so, because I think how they work is having 2 different metals that expand at different rates, and I'm guessing the tip is where the 2 metals meet.
2) Does anyone know what the shortest length needed to protect the wire connections from the forge heat? I'm currently using a 12" TC, but with only 2-3 inches in the forge, I have 6-7 inches hanging out the back of my forge, which is mildly inconvenient.
Thank you.
I noticed my TC is starting to wear out, and am planning on ordering a couple to have on back-up.
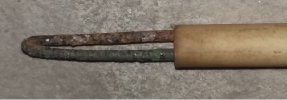
1) Is it possible to cut the corroded portion off, and if there's enough left, bend the remaining portion into a U and use? I don't think so, because I think how they work is having 2 different metals that expand at different rates, and I'm guessing the tip is where the 2 metals meet.
2) Does anyone know what the shortest length needed to protect the wire connections from the forge heat? I'm currently using a 12" TC, but with only 2-3 inches in the forge, I have 6-7 inches hanging out the back of my forge, which is mildly inconvenient.
Thank you.