DanF
Knifemaker / Craftsman / Service Provider
- Joined
- Apr 17, 2017
- Messages
- 1,411
Well, I know Charles says it can be done, but I had to see for myself (not doubting Charles, but sometimes you just gotta try something new, you know?), so I had some short cutoffs in the scrap bucket and decided to see what this diminutive little forge could do.
I took three pieces of .120 15n20 and two pieces of 1084, all of them 1" x 4", welded the edges and stuck them in the forge. FORGE welded them together, started drawing them out to 5/8"x5/8", rounded the corners and put a couple twists on them. Five minutes in FeCl and now I can say, "yeah, it forges and here's the proof."
I know there are grind lines in there, this was just some experimentation with some scraps. Loving this little forge more and more. Bigger would be better, but man it SIPS! Oh, I think I just fell down a rabbit hole with pattern welding, I really need a power hammer for sure now.
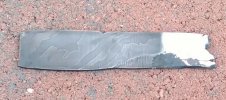
I took three pieces of .120 15n20 and two pieces of 1084, all of them 1" x 4", welded the edges and stuck them in the forge. FORGE welded them together, started drawing them out to 5/8"x5/8", rounded the corners and put a couple twists on them. Five minutes in FeCl and now I can say, "yeah, it forges and here's the proof."
I know there are grind lines in there, this was just some experimentation with some scraps. Loving this little forge more and more. Bigger would be better, but man it SIPS! Oh, I think I just fell down a rabbit hole with pattern welding, I really need a power hammer for sure now.
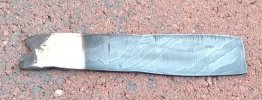
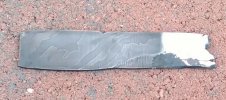