- Joined
- Jan 14, 2020
- Messages
- 27
Hi all,
I recently got an order for a champagne saber. I have only been making knives for about one and a half year now, so this totally blew me away. I accepted the order and decided to do this one by stock removal. I cut the blank out of 14C28N stainless steel, and I have a few questions I would like to ask of more experienced makers than myself.
Firstly, a bit more info on the blade:
I would like your opinion on the following things:
1. What type of edge should I grind on? It seems to me that the example above has no grind/bevel at all. What do you think? To saber a champagne bottle successfully, a dull or just square edge must be used, as the glass will damage a sharp and thin edge. I plan to put a distal taper on the blade so that at least the tip is sharp and not square. 2.5mm is quite thick to leave it unground without a bevel, so I think I should maybe put a flat grind on it and leave the edge 1 - 1.5mm thick. (By the way, I have no contact wheels so hollow grinds are not an option.) I could also thin the edge a bit by putting a convex grind on and blending it in so that no plunge line is visible. I would like to hear your thoughts on this.
2. I do not know how I should heat treat this blade. I have no heat treating ovens or anything, just a forge and a quench tank filled with vegetable oil. I have successfully quenched 14C28N blades before that were smaller and about 4mm thick. I am a bit scared that this thin a blade would warp easily in such a basic quench. I could just not heat treat it at all and leave it soft, as it will not have a sharp edge, but then it would probably bend when used. I know that blades can be straightened in the temper by clamping them to a straight object. I really need your help on this.
A few bits of stray information:
I look forward to hearing from you! Please respond quickly!
Thank you in advance,
Reuben
I recently got an order for a champagne saber. I have only been making knives for about one and a half year now, so this totally blew me away. I accepted the order and decided to do this one by stock removal. I cut the blank out of 14C28N stainless steel, and I have a few questions I would like to ask of more experienced makers than myself.
Firstly, a bit more info on the blade:
- Made of 2.5mm (about 3/32 inch I think) thick 14C28N stainless steel.
- The design is really simple. It literally looks like a huge trailing point knife and is 45 cm (about 17.5 inch) long overall. The blade is 45mm wide (1.7 inch). There is no guard or anything, only a normal full tang handle. This example looks almost exactly like the one that I am making:
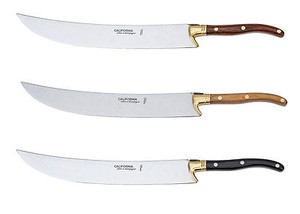
I would like your opinion on the following things:
1. What type of edge should I grind on? It seems to me that the example above has no grind/bevel at all. What do you think? To saber a champagne bottle successfully, a dull or just square edge must be used, as the glass will damage a sharp and thin edge. I plan to put a distal taper on the blade so that at least the tip is sharp and not square. 2.5mm is quite thick to leave it unground without a bevel, so I think I should maybe put a flat grind on it and leave the edge 1 - 1.5mm thick. (By the way, I have no contact wheels so hollow grinds are not an option.) I could also thin the edge a bit by putting a convex grind on and blending it in so that no plunge line is visible. I would like to hear your thoughts on this.
2. I do not know how I should heat treat this blade. I have no heat treating ovens or anything, just a forge and a quench tank filled with vegetable oil. I have successfully quenched 14C28N blades before that were smaller and about 4mm thick. I am a bit scared that this thin a blade would warp easily in such a basic quench. I could just not heat treat it at all and leave it soft, as it will not have a sharp edge, but then it would probably bend when used. I know that blades can be straightened in the temper by clamping them to a straight object. I really need your help on this.
A few bits of stray information:
- I plan to do all grinding after heat treatment (if it is gonna happen). This way I can leave the blade as thick as possible going into the quench.
- The blade due date is 28 February, so time is not in excess here!!
- The blade will have a 800 grit hand sanded finish.
I look forward to hearing from you! Please respond quickly!
Thank you in advance,
Reuben