I worked on this one off and on for a few months, just a little bit at a time, learning as I went. This was my first, and so far only attempt to create a new folding knife blade. Admittedly, this should be looked at as a "quick and dirty" version, because my main focus was to make sure that I could make everything fit and function. Finish was secondary concern at best. Customer versions will be better finished.
Spyderco Resilience, AEB-L reblade (new blade shape as well), 63 RC, custom G10 handle scales:
I measured and plotted the blade out in CAD, and then had Jarod plasma cut and heat treat it. It can admittedly be improved a bit from here, specifically with regard to the detent hole. I misplaced it by about a half a millimeter, which you can see in the detent action in the video below by how loose the blade is in close position:
Nevertheless, it doesn't poke out past the scales, so safety is not impeded. And f course, this will be corrected on the next run.
But with much of the learning curve behind me I and how it turned out for a first attempt, I believe I am almost ready to start offering this skill to the community. So I'm planning a small run of rebladed Resilience knives in AEB-L. Why Resiliences? Because I like the size, strength, and lock up of the Resilience. And also after doing this knife, I realize a few things: I could make a knife with a completely different blade and handle shape, including a smaller and yes even larger blade and handle, using the Spyderco liners and hardware as a base. How? I can mod the liners and make new scales to create a folder version of a partial tang knife, except it would be partial liners. So I could turn a 4 1/4" Resilience knife into a 6" bladed fighter, and simply cut the steel liners square and then make scales with white G10 liners that fill up the space where the steel liners are too short or narrow. And finally we will have mega folders that have both opening holes and tip down as an options (customers can specify their preferred clip hole placement, of course). I will make at least one of these for myself as a proof of concept, like I made the knife pictured here to prove to myself that I could actually rescale and reblade a liner locking folding knife. And you can bet my mega folder will be AEB-L at around 61 RC for that great balance of corrosion resistance and fine edge stability with great toughness.
Also, this saves me from having to invest further time into designing a "skeleton" for the knife, and figuring out hardware, etc. I am sure I will do this eventually, but for now, because I can make fully custom folders of any shape or size using the Resilience as a platform, I will. I'm sure Spyderco won't begrudge me the revenue if I buy half a dozen or a dozen folders.
BUT, this idea is in its infancy, and is a medium term project at best this point, so I can't say I expect anything will be built or ready (other than the knife above) until at least half a year down the road. That being said, the more interest there is in this from the community, then the faster things will likely get moving. So if you are interested in a David Mary Custom folder with cannibalized Spyderco guts, then get in touch via PM or email, and we'll talk about your own custom folder design. In the meantime, I will update this thread periodically with whatever I decide to come up with for myself, which will definitely include a mega folder, and also perhaps a re-visitation of the hitherto ill-fated
Astrid.
Please remember the pics below represent a roughed out prototype, a customer version will have a better finished handle (just needs a bit more hand sanding) and also the aforementioned detent issue corrected. Also, handle available will include thick scales, thin scales, and any finish style I have done to date, including flat, contouring, any of the textured styles I have done, or contoured plus texture. Also note the opening hole is not an exact circle. This is to avoid conflicting with Spyderco's trademarked round hole. On subsequent models, this lack of perfect circularity will be made a little bit more obvious to remove possible doubt.
Thanks for looking!
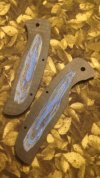