Stacy E. Apelt - Bladesmith
ilmarinen - MODERATOR
Moderator
Knifemaker / Craftsman / Service Provider
- Joined
- Aug 20, 2004
- Messages
- 37,721
I was asked to post a tutorial to explain and show how to build a diagonally braced workbench. The main thing about it is it has no vertical legs to get in the way. It is as strong as a vertical leg bench if built right.
First, here is why it works:
A triangle is the only geometrical structure that cannot be compressed. No matter how much force is applied to any side or corner it will not change shape. An inverted right triangle is what we are using in this bench construction. The wall studs in your shop are the vertical side, the bench top brace is the horizontal side, and the diagonal brace is the hypotenuse. The only way it will change shape is by catastrophic collapse. Using normal dimensional lumber and proper technique it should be rock solid for our uses. They build houses on cliffs using the same technique.
1) The wall studs - I left the sister boards out the first time. I added them and redrew the sketches.
The studs need to be exposed for attaching the braces.
Because the two braces screw to each other, you need to add a spacer board to each wall stud at the diagonal brace to move it in alignment with the wall stud. Cut the boards to fit from the footer to the bottom of the top brace. Screw and glue this to the wall stud. Screw the top brace to the wall stud and diagonal brace to the sister board. You should use 4" screws at the diagonal brace so the screws go into the stud through the sister board. Drilling pilot holes is wise.
If you are working on a wall that is already covered with sheetrock this creates a little problem. You will need cut away the sheetrock from the top brace to the footer board. You can put a patch board over it later or just let it be.
2) The top and diagonal brace -
Use 2X6 select grade or #1 grade lumber. If you want a really solid bench use 2X8s.
The diagonal brace can be increased to 2X10 or 2X12 if you are adding a shelf below the top. The wider the diagonal brace the stronger the assembly. See diagram.
3) The bench top -
The bench top I like is 2X6 lumber with a plywood cover. It can be made with 2X8s, 2X10s, or 2X12s if that is what you have laying around. Obviously a 2X6 is strong enough on its own, but putting a piece of 1/2" (or thicker) plywood over the 2X6 top makes it cleaner and gets rid of the cracks. You don't need a bench this solid, but you will love it if you make one. I put 20-gauge stainless sheet metal on top of my benches.
If building a lighter duty hobby bench you can just use a sheet of 3/4" plywood and skip the 2X6s.
4) Construction -
Use good construction grade screws. I use torx-drive 3.5" and 4" #9 construction screws. I like to use Tightbond glue on the joints as well. Not required, but just one more thing to add strength. For the low cost of a bottle of glue I would say it is a no brainer.
Space the braces at 48" spacing for a normal bench or at 32" for a bench with heavy stuff on it. Obviously, you need to fit the spacing of the studs. The bench top can extend past the top braces about 6-8" with no harm. If making a bench wall-to-wall, just screw the end braces directly to the side wall studs. No need for diagonals there.
5) Face board and backboard-
The face board is what people will see first when they look at your bench. A face board makes the whole bench stronger and nicer looking as well as allows the attachment of certain vices and tooling. One of the biggest things it does is covers the joints of the braces, 2X6 top, and plywood cap cleanly. You want the prettiest and cleanest 2X6 you can find for this. If you will do a lot of work at the bench a 2X6 oak or maple board is not a bad idea. Both the top brace and the diagonal brace should meet pretty perfect at the front for the face board to fit right. You should make the face board just slightly proud of the bench top. This keeps things from rolling off the bench. 1/16" inch is plenty.
6) Backboard -
If the wall will be bare studs after the bench is up, put at least a 1X12 backboard on the studs after the bench is done. If you don't everything you set on the bench will mysteriously disappear down the back side gap. I would suggest that it be a full width piece of plywood. That way you can screw on shelves, hooks, etc. Or, put the sheetrock up after building the bench.
Construction method:
A) Start by cutting all the top braces. Temporarily mount one to the stud at the desired height. Use two screws to hold it roughly level.
What I do next is cut the end of the diagonal brace that fits at the wall and footer and leave the other end uncut and a little longer than needed.
I attach with one screw at the wall stud and then, using a level, with one screw at the top brace. Once all is square and level, I draw the cut lines on the diagonal and remove it for cutting. This assures an exact fit to the top brace. Cut it out on the lines you drew and re-mount to check. If everything fits pretty good at both ends, remove it and use it as a pattern to make the other diagonal braces. There can be a little misalignment at the footer, but you do not want the diagonal brace sticking out past the top brace on the front or top. Once all braces are cut, glue and screw everything together.
B) Next, cut and fit the 2X6 top boards. The boards can end flush with the top brace sides or extend past them up to 8" with no problem.
Start with the board at the front edge. Make it align with the front of the top brace as close as possible. I temporarily screw a 2X6 to the front of the braces so it sticks up an inch or more above the top brace. This allows the first board to be fitted flush easily. Add the next boards tight to each other as you go toward the wall. The last board may need to be cut narrower and sometimes even tapered a bit to fit snug against the studs.
C) Putting on the top surface - Lay the plywood on the bench top good side down, push back snug to the studs, and mark the front and sides with a pencil from below. Cut the plywood on the lines. Flip 180° and put on with the factory edge at the front. Plane or sand flush with the front and sides if needed. Align the front edge closely with the 2X6 top.
D) Face Boards and End Boards - Screw on the 2X6 face board so it is just ever so slightly proud of the plywood top. Just enough to feel with your fingertips. If the bench does not go from wall to wall adding end boards that stick up a few inches above the bench is a good idea. Use 2X8 lumber for end boards.
Brace spacing: Added information
The braces need to be frequent enough to carry the load of the benchtop and equipment. On a light duty hobby and drafting bench just at the ends will work. On a regular shop bench every 32" is better. One way to make an 8 foot bench with only one middle brace and the end braces is to use double top braces. Make two top braces for every diagonal brace. Put a top brace on each side of the wall stud and the diagonal brace between them. The diagonal brace in this setup goes all the way to the floor and against the wall stud. Put two sister boards on each side of the diagonal brace at the wall stud. These sister boards should be 2X6 and go up to the top braces. You will need to notch the bottom of the sister boards to fit against the footer and the floor. This method can be used for any length bench. I have a 13' and a 14' wall-to-wall bench with only two braces with the ends on 2X8 ledger boards screwed to the end walls. I added a sketch of the double brace setup.
Here are the drawings:
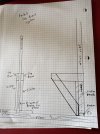
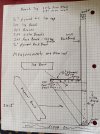
First, here is why it works:
A triangle is the only geometrical structure that cannot be compressed. No matter how much force is applied to any side or corner it will not change shape. An inverted right triangle is what we are using in this bench construction. The wall studs in your shop are the vertical side, the bench top brace is the horizontal side, and the diagonal brace is the hypotenuse. The only way it will change shape is by catastrophic collapse. Using normal dimensional lumber and proper technique it should be rock solid for our uses. They build houses on cliffs using the same technique.
1) The wall studs - I left the sister boards out the first time. I added them and redrew the sketches.
The studs need to be exposed for attaching the braces.
Because the two braces screw to each other, you need to add a spacer board to each wall stud at the diagonal brace to move it in alignment with the wall stud. Cut the boards to fit from the footer to the bottom of the top brace. Screw and glue this to the wall stud. Screw the top brace to the wall stud and diagonal brace to the sister board. You should use 4" screws at the diagonal brace so the screws go into the stud through the sister board. Drilling pilot holes is wise.
If you are working on a wall that is already covered with sheetrock this creates a little problem. You will need cut away the sheetrock from the top brace to the footer board. You can put a patch board over it later or just let it be.
2) The top and diagonal brace -
Use 2X6 select grade or #1 grade lumber. If you want a really solid bench use 2X8s.
The diagonal brace can be increased to 2X10 or 2X12 if you are adding a shelf below the top. The wider the diagonal brace the stronger the assembly. See diagram.
3) The bench top -
The bench top I like is 2X6 lumber with a plywood cover. It can be made with 2X8s, 2X10s, or 2X12s if that is what you have laying around. Obviously a 2X6 is strong enough on its own, but putting a piece of 1/2" (or thicker) plywood over the 2X6 top makes it cleaner and gets rid of the cracks. You don't need a bench this solid, but you will love it if you make one. I put 20-gauge stainless sheet metal on top of my benches.
If building a lighter duty hobby bench you can just use a sheet of 3/4" plywood and skip the 2X6s.
4) Construction -
Use good construction grade screws. I use torx-drive 3.5" and 4" #9 construction screws. I like to use Tightbond glue on the joints as well. Not required, but just one more thing to add strength. For the low cost of a bottle of glue I would say it is a no brainer.
Space the braces at 48" spacing for a normal bench or at 32" for a bench with heavy stuff on it. Obviously, you need to fit the spacing of the studs. The bench top can extend past the top braces about 6-8" with no harm. If making a bench wall-to-wall, just screw the end braces directly to the side wall studs. No need for diagonals there.
5) Face board and backboard-
The face board is what people will see first when they look at your bench. A face board makes the whole bench stronger and nicer looking as well as allows the attachment of certain vices and tooling. One of the biggest things it does is covers the joints of the braces, 2X6 top, and plywood cap cleanly. You want the prettiest and cleanest 2X6 you can find for this. If you will do a lot of work at the bench a 2X6 oak or maple board is not a bad idea. Both the top brace and the diagonal brace should meet pretty perfect at the front for the face board to fit right. You should make the face board just slightly proud of the bench top. This keeps things from rolling off the bench. 1/16" inch is plenty.
6) Backboard -
If the wall will be bare studs after the bench is up, put at least a 1X12 backboard on the studs after the bench is done. If you don't everything you set on the bench will mysteriously disappear down the back side gap. I would suggest that it be a full width piece of plywood. That way you can screw on shelves, hooks, etc. Or, put the sheetrock up after building the bench.
Construction method:
A) Start by cutting all the top braces. Temporarily mount one to the stud at the desired height. Use two screws to hold it roughly level.
What I do next is cut the end of the diagonal brace that fits at the wall and footer and leave the other end uncut and a little longer than needed.
I attach with one screw at the wall stud and then, using a level, with one screw at the top brace. Once all is square and level, I draw the cut lines on the diagonal and remove it for cutting. This assures an exact fit to the top brace. Cut it out on the lines you drew and re-mount to check. If everything fits pretty good at both ends, remove it and use it as a pattern to make the other diagonal braces. There can be a little misalignment at the footer, but you do not want the diagonal brace sticking out past the top brace on the front or top. Once all braces are cut, glue and screw everything together.
B) Next, cut and fit the 2X6 top boards. The boards can end flush with the top brace sides or extend past them up to 8" with no problem.
Start with the board at the front edge. Make it align with the front of the top brace as close as possible. I temporarily screw a 2X6 to the front of the braces so it sticks up an inch or more above the top brace. This allows the first board to be fitted flush easily. Add the next boards tight to each other as you go toward the wall. The last board may need to be cut narrower and sometimes even tapered a bit to fit snug against the studs.
C) Putting on the top surface - Lay the plywood on the bench top good side down, push back snug to the studs, and mark the front and sides with a pencil from below. Cut the plywood on the lines. Flip 180° and put on with the factory edge at the front. Plane or sand flush with the front and sides if needed. Align the front edge closely with the 2X6 top.
D) Face Boards and End Boards - Screw on the 2X6 face board so it is just ever so slightly proud of the plywood top. Just enough to feel with your fingertips. If the bench does not go from wall to wall adding end boards that stick up a few inches above the bench is a good idea. Use 2X8 lumber for end boards.
Brace spacing: Added information
The braces need to be frequent enough to carry the load of the benchtop and equipment. On a light duty hobby and drafting bench just at the ends will work. On a regular shop bench every 32" is better. One way to make an 8 foot bench with only one middle brace and the end braces is to use double top braces. Make two top braces for every diagonal brace. Put a top brace on each side of the wall stud and the diagonal brace between them. The diagonal brace in this setup goes all the way to the floor and against the wall stud. Put two sister boards on each side of the diagonal brace at the wall stud. These sister boards should be 2X6 and go up to the top braces. You will need to notch the bottom of the sister boards to fit against the footer and the floor. This method can be used for any length bench. I have a 13' and a 14' wall-to-wall bench with only two braces with the ends on 2X8 ledger boards screwed to the end walls. I added a sketch of the double brace setup.
Here are the drawings:
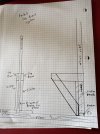
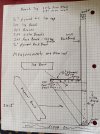
Last edited: