The difference is that we don't have to be was picky as say Gibson when they are looking for an AAA+++ book matched top slab for Custom Shop Les Paul. We can use small "scrap" pieces that can even appear in an otherwise straight grain plank. Likewise the wood with the BIG flamey stripes as wide as your finger are great for an electric guitar top or acoustic stringed instrument sides and back, but not so much for a little knife handle. Same with woods like black walnut. We can get wonderful looking pieces in knife handle block or scale sizes, but it would be more difficult to find a piece that nice in sizes suitable for a rifle stock or some piece of furniture. As for coloring, if you want it darker and stabilized, get it dyed.
Here are a couple of examples of the "wide" flame" maple that I was talking about.
Recent Custom Shop Gibson Les Paul R9
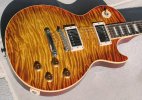
Late 80's Paul Reed Smith guitar with a "10 top"
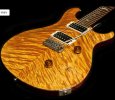
You can see that he wood used on both of these guitars might get lost on something as small as a knife handle, but is "grail wood" for a maple top solid body electric guitar. :thumbup:
Here is an interesting little factoid about dying maple. Both of those newer guitars are dyed to look like what a 1958-59 Gibson cherry sunburst Les Paul would have looked like after a number of years of fading. The guitar would have originally been red around the edges and faded to the lighter color in the middle, hence the name "sunburst" for the finish. The problem is that the red dye faded badly under UV light. You can see on the Gibson how they blended a very faint wash of the red dye around the edge of the top to really give it that faded effect. Gibson had previous only done "brown" sunburst finishes now called tobacco or ice tea burst, so this was a surprise for them. The legend goes that some music stores put these guitars in their front window to show them off and the sun caused them to fade VERY quickly. They changed red dyes in 1960, the last year of the original run for the Les Paul, so the 1960's "bursts" will still have a lot of red, but not the '58 or "59 models. The funny part is if you remove the title plastic plate that surrounds the switch on a '59, it will still be very dark red underneath. Same thing to a great degree on all of the '58's and most of the 59's that had pick guards. Of course, nowadays, the best examples of these "defective" instruments from that late '50's sell for over $500,000!!!!!!