Cushing H.
Gold Member
- Joined
- Jun 3, 2019
- Messages
- 2,714
In working on handles for a knife yesterday, it became stunningly clear to me that I was placing undue belief (read as "stupid") in thinking that I could drill out a central hole for corby bolts, then hand-drill the larger hole by sight. Second time I have tried this, and the second time I had a mis-alignment. so, away I go in looking at step drills from on line sites. they are EXPENSIVE, and I would need to wait for shipping. Lacking any local alternative to buy something, I started looking on line, and ended up studying Walter Sorrells "50 ways to make a step drill." (
). My guess is that this is an old discussion ... but as I ran across at least one old thread where people said "dont make your own, buy from the supply shop selling the bolts", I thought I would share this.
Given the low expense (just a few $$), and the alternative of a long wait for shipping from a supplier I decided to try my hand at making my own. If you look at Walter's video, he discusses making a "twiddle fixture" to hold a drill bit both parallel and at a uniform distance from a grinder belt, then turning ("twiddling") the bit so as to uniformly decrease the circumference of some section of the tip (so as to maintain concentricity of both the large and small diameters. Literally just a couple minutes to drill the "fixture", a couple minutes to set up markers (really tape) on the work rest, and something like 5-10 minutes grinding the drill bit, and I got this:
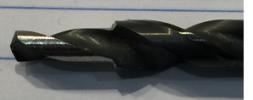
He is right - it could be really easy to overshot the grind and end up with too small a circumference - but this one I actually hit to the mil. He is also right that the shoulder is not perfectly flat ... but likely good enough - and he is also right that it would be pretty easy to take a dremmel grinding disk and flatten out that shoulder.
Really cool - saved something like $30, and I get to finish this knife this week!
Given the low expense (just a few $$), and the alternative of a long wait for shipping from a supplier I decided to try my hand at making my own. If you look at Walter's video, he discusses making a "twiddle fixture" to hold a drill bit both parallel and at a uniform distance from a grinder belt, then turning ("twiddling") the bit so as to uniformly decrease the circumference of some section of the tip (so as to maintain concentricity of both the large and small diameters. Literally just a couple minutes to drill the "fixture", a couple minutes to set up markers (really tape) on the work rest, and something like 5-10 minutes grinding the drill bit, and I got this:
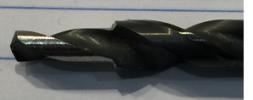
He is right - it could be really easy to overshot the grind and end up with too small a circumference - but this one I actually hit to the mil. He is also right that the shoulder is not perfectly flat ... but likely good enough - and he is also right that it would be pretty easy to take a dremmel grinding disk and flatten out that shoulder.
Really cool - saved something like $30, and I get to finish this knife this week!