Sort of an anouncement since they have been available since the begining of May, but still waiting for EP to get them on their website. EP has expanded the polishing stone lineup to include 300, 650, and 1100 mesh resin bond diamond stones. The purpose of this thread is I, the developer and manufacturer of these stones, would like to get some feedback on them as well as some unbiased opinions. To do this I will be making a kit of a full set of stones, plus a few extras, a flat plate, and some loose abrasive to dress them as needed. These will be my personal set so they are not cosmetically first quality but the resin/diamond mix is the same. I will offer this kit as a pass-around. The only cost to try them out is the postage to send it to the next recipient, and to post your honest thoughts about them in this thread. I will make the kit fit in a USPS Medium Flat Rate box so $13.65. Link to the pass-around thread Here.
Who am I. I first met Ben when he was looking for someone to make the mold for the Apex back in 1994. We made a deal, he paid a down payment, and I bought a used manual milling machine and lathe, and then made the mold at home in my spare time since I had a day job. Soon after making the mold I had a range fire, I live in the country, that burned my shop to the ground. When I rebuilt I got a cnc mill and with those capabilities I started making the scissor sharpener parts around 2000 or so. A few years ago I made some resin bond polishing stones for EP to try out. Not a big deal since I had been making something similar for years to polish stone. At first they didn't like them, but they really liked the machined polishing tape holders I made to test the tapes with, then after a few months EP found themselves using the polishing stones over the tapes for in-house knife sharpening, which became their polishing stones. I am a business that manufactures a few items for EP and I also make my own products that I sell direct with my own website here.
So, about the stones. The grits in the kit will be 80 grit -160 micron, 250-80 micron, 600-35 micron, 1100-17 micron, 2300-8 micron, 4000-5 micron, and 6500-4 micron. They are a .062" resin bond diamond matrix with a .188" thick aluminum back, for a total thickness of .25". The backs are flat within .001" total deviation and the resin surface is flat within about .0003" as molded. The exact thickness of the finished stone can vary by around .004" for the finer stones, and up to .015" for the 80. The larger the grit the more it may vary because diamond crystals can get between the aluminum back and the mold when molding them, just the nature of the process. The diamond is very high quality monocrystalin that is processed here in the US. I have been buying from the same supplier for about 15 years now. I mix about as much diamond into the resin as possible, more just increases the wear rate of the stones without making them any more aggressive. I make the stones I want to use, no corners are cut. They are pretty low wear, how low depends on how much pressure is used when sharpening. In 6 months the samples I gave to EP have worn around .002"-.004" and they have sharpened hundreds of knives. The 300 grit stone has worn around .005" and sharpened around 30 knives. Be real careful with the pressure on the 250 or 300 grit stones as they can wear quickly, I wore .004" off my 250 doing a restoration job on 2 of my my neighbors cheap gooey steel chef knives by using too much pressure. I should have just used the Sic stones for that job as the steel was just too soft. The harder the material you are sharpening the better they work, including ceramic, and the slower they wear. This is especially true for the finer grit stones. The 6500 should only be used on the hardest steels or ceramic, anything less don't go past the 4000, sometimes don't go past the 2300. As I have said on this forum before, don't put too much value in the numbers on the stones, they don't mean very much. There are many factors that determin how a stone works, the bond is as important as the abrasive size. This is a resin bond, a rather unique resin bond. Keep an open mind when testing them.
I was at EP yesterday afternoon so I measured the thickness of their diamond stones and engraved it on the back of all of them so I can track the wear accuratly. The 2300 they have been using since 5-16 has worn .005", and they use it all the time. Granted there was a second 2300 added at some point, I removed it, but still EP sharpens a lot of knives and most of the wear was from too much dressing. With proper care all but the coarsest stone should last a lifetime of home use, and maybe a lifetime of professional use for the finer grits.
How to use the stones. These stones are non-pourous but seem to hold the water fairly well. I use a cup of water that I dip my finger in to wet the stone. A little soap would be good but I almost never think of it. Use very low pressure even for a larger bevel, none for smaller bevels, and be very carful with the stone when just starting a bevel to keep the point loading low. Absolutely no pressure for the 2300 and up stones, they don't need it. For the 2300 and up only use the weight of the stone and stone holder! All a little pressure will do is make you need to dress them sooner. I will use both edge leading and trailing passes with up to the 1100 stone. Above that edge trailing only!!!! I find that edge leading passes increase microchipping which then scratch the bevel. The grit progression is designed for 10 passes on a 3-1/2" CRKT 440c blade with about a .1" wide bevel. I did this myself with my microscope so I could see what was really happening. Without the microscope I increase the passes by around 50% to make sure the blade is ready for the next grit. Keep the swarf cleaned up and clean it off your knife and the sharpener before moving to the next grit. You don't want to contaminate the new stone with the swarf from the last one. The swarf should only be steel fillings, as long as you keep the pressure light. With the 2300 and up be methodical and careful, do the 10 ish passes and move on. These stones really just polish out the scratches from the last grit, but they will make your knife noticably sharper than the last grit. Generally you will still have a hazy polish with these stones, unless your steel is extremely hard and fine grained. They rarely give that mirror polish. Next up is some leather and make up my own diamond polishing compound to improve the polish. If it works you might find that in the kit as well. It seems to me that these stones leave noticeably less of a burr than Alox stones, the 2300 and up don't seem to leave a noticeable burr.
Dressing and other maintenance. The 250 and 300 stones shouldn't need dressing. With light pressure the swarf will wear the resin away exposing the diamond. They will probably only need to be dressed to fix dishing, which should take a long time. The 600 and 1100 I am not sure about. The 2300 and up need to be dressed when they start scratching more than when freshly dressed. Best case every 10-20 knives. The finer the grit the fussier they are. The 6500 is very fussy so that is why it hasn't made it to production. Use rubbing alcohol with a paper towel or cloth to clean the stones between dressings. The coarsest stones don't ever need cleaning, the finest need it the most often. DO NOT use any other chemicals on them, some will attack the resin.
Here is an interesting test to see if there is a difference whether using Alox or CBN/Diamond to sharpen with. Link
Here are some photos. Finest grit at the top, coarsest at the bottom. The 2300 and 4000 have some pinholes. I have not noticed the pinholes causing any issues in the last 25 months even though I am looking for them. I can not guarantee the resin bond stones I make are 100% free of porosity, just the way I make them, fact of life.
The 6500 is the only back that is current, the rest are old production or prototypes. I engraved the thickness and date on all of them so we can track wear. I measured them right in the center where I engraved the O.
Here is an up close look at the 250.
Shot of the 300 mesh stone under the microscope. The amount of diamond by weight is pretty consistent between the different grits so the finer grits show even more diamond to resin ratio.
This is how I measure the blanks for deviation from the reference surface.
This is the machine I use to make everything on. The width of all the aluminum backs are within +/-.0001" from each other, doesn't need to be, just how accurate the mill is.
Who am I. I first met Ben when he was looking for someone to make the mold for the Apex back in 1994. We made a deal, he paid a down payment, and I bought a used manual milling machine and lathe, and then made the mold at home in my spare time since I had a day job. Soon after making the mold I had a range fire, I live in the country, that burned my shop to the ground. When I rebuilt I got a cnc mill and with those capabilities I started making the scissor sharpener parts around 2000 or so. A few years ago I made some resin bond polishing stones for EP to try out. Not a big deal since I had been making something similar for years to polish stone. At first they didn't like them, but they really liked the machined polishing tape holders I made to test the tapes with, then after a few months EP found themselves using the polishing stones over the tapes for in-house knife sharpening, which became their polishing stones. I am a business that manufactures a few items for EP and I also make my own products that I sell direct with my own website here.
So, about the stones. The grits in the kit will be 80 grit -160 micron, 250-80 micron, 600-35 micron, 1100-17 micron, 2300-8 micron, 4000-5 micron, and 6500-4 micron. They are a .062" resin bond diamond matrix with a .188" thick aluminum back, for a total thickness of .25". The backs are flat within .001" total deviation and the resin surface is flat within about .0003" as molded. The exact thickness of the finished stone can vary by around .004" for the finer stones, and up to .015" for the 80. The larger the grit the more it may vary because diamond crystals can get between the aluminum back and the mold when molding them, just the nature of the process. The diamond is very high quality monocrystalin that is processed here in the US. I have been buying from the same supplier for about 15 years now. I mix about as much diamond into the resin as possible, more just increases the wear rate of the stones without making them any more aggressive. I make the stones I want to use, no corners are cut. They are pretty low wear, how low depends on how much pressure is used when sharpening. In 6 months the samples I gave to EP have worn around .002"-.004" and they have sharpened hundreds of knives. The 300 grit stone has worn around .005" and sharpened around 30 knives. Be real careful with the pressure on the 250 or 300 grit stones as they can wear quickly, I wore .004" off my 250 doing a restoration job on 2 of my my neighbors cheap gooey steel chef knives by using too much pressure. I should have just used the Sic stones for that job as the steel was just too soft. The harder the material you are sharpening the better they work, including ceramic, and the slower they wear. This is especially true for the finer grit stones. The 6500 should only be used on the hardest steels or ceramic, anything less don't go past the 4000, sometimes don't go past the 2300. As I have said on this forum before, don't put too much value in the numbers on the stones, they don't mean very much. There are many factors that determin how a stone works, the bond is as important as the abrasive size. This is a resin bond, a rather unique resin bond. Keep an open mind when testing them.
I was at EP yesterday afternoon so I measured the thickness of their diamond stones and engraved it on the back of all of them so I can track the wear accuratly. The 2300 they have been using since 5-16 has worn .005", and they use it all the time. Granted there was a second 2300 added at some point, I removed it, but still EP sharpens a lot of knives and most of the wear was from too much dressing. With proper care all but the coarsest stone should last a lifetime of home use, and maybe a lifetime of professional use for the finer grits.
How to use the stones. These stones are non-pourous but seem to hold the water fairly well. I use a cup of water that I dip my finger in to wet the stone. A little soap would be good but I almost never think of it. Use very low pressure even for a larger bevel, none for smaller bevels, and be very carful with the stone when just starting a bevel to keep the point loading low. Absolutely no pressure for the 2300 and up stones, they don't need it. For the 2300 and up only use the weight of the stone and stone holder! All a little pressure will do is make you need to dress them sooner. I will use both edge leading and trailing passes with up to the 1100 stone. Above that edge trailing only!!!! I find that edge leading passes increase microchipping which then scratch the bevel. The grit progression is designed for 10 passes on a 3-1/2" CRKT 440c blade with about a .1" wide bevel. I did this myself with my microscope so I could see what was really happening. Without the microscope I increase the passes by around 50% to make sure the blade is ready for the next grit. Keep the swarf cleaned up and clean it off your knife and the sharpener before moving to the next grit. You don't want to contaminate the new stone with the swarf from the last one. The swarf should only be steel fillings, as long as you keep the pressure light. With the 2300 and up be methodical and careful, do the 10 ish passes and move on. These stones really just polish out the scratches from the last grit, but they will make your knife noticably sharper than the last grit. Generally you will still have a hazy polish with these stones, unless your steel is extremely hard and fine grained. They rarely give that mirror polish. Next up is some leather and make up my own diamond polishing compound to improve the polish. If it works you might find that in the kit as well. It seems to me that these stones leave noticeably less of a burr than Alox stones, the 2300 and up don't seem to leave a noticeable burr.
Dressing and other maintenance. The 250 and 300 stones shouldn't need dressing. With light pressure the swarf will wear the resin away exposing the diamond. They will probably only need to be dressed to fix dishing, which should take a long time. The 600 and 1100 I am not sure about. The 2300 and up need to be dressed when they start scratching more than when freshly dressed. Best case every 10-20 knives. The finer the grit the fussier they are. The 6500 is very fussy so that is why it hasn't made it to production. Use rubbing alcohol with a paper towel or cloth to clean the stones between dressings. The coarsest stones don't ever need cleaning, the finest need it the most often. DO NOT use any other chemicals on them, some will attack the resin.
Here is an interesting test to see if there is a difference whether using Alox or CBN/Diamond to sharpen with. Link
Here are some photos. Finest grit at the top, coarsest at the bottom. The 2300 and 4000 have some pinholes. I have not noticed the pinholes causing any issues in the last 25 months even though I am looking for them. I can not guarantee the resin bond stones I make are 100% free of porosity, just the way I make them, fact of life.

The 6500 is the only back that is current, the rest are old production or prototypes. I engraved the thickness and date on all of them so we can track wear. I measured them right in the center where I engraved the O.

Here is an up close look at the 250.

Shot of the 300 mesh stone under the microscope. The amount of diamond by weight is pretty consistent between the different grits so the finer grits show even more diamond to resin ratio.

This is how I measure the blanks for deviation from the reference surface.

This is the machine I use to make everything on. The width of all the aluminum backs are within +/-.0001" from each other, doesn't need to be, just how accurate the mill is.
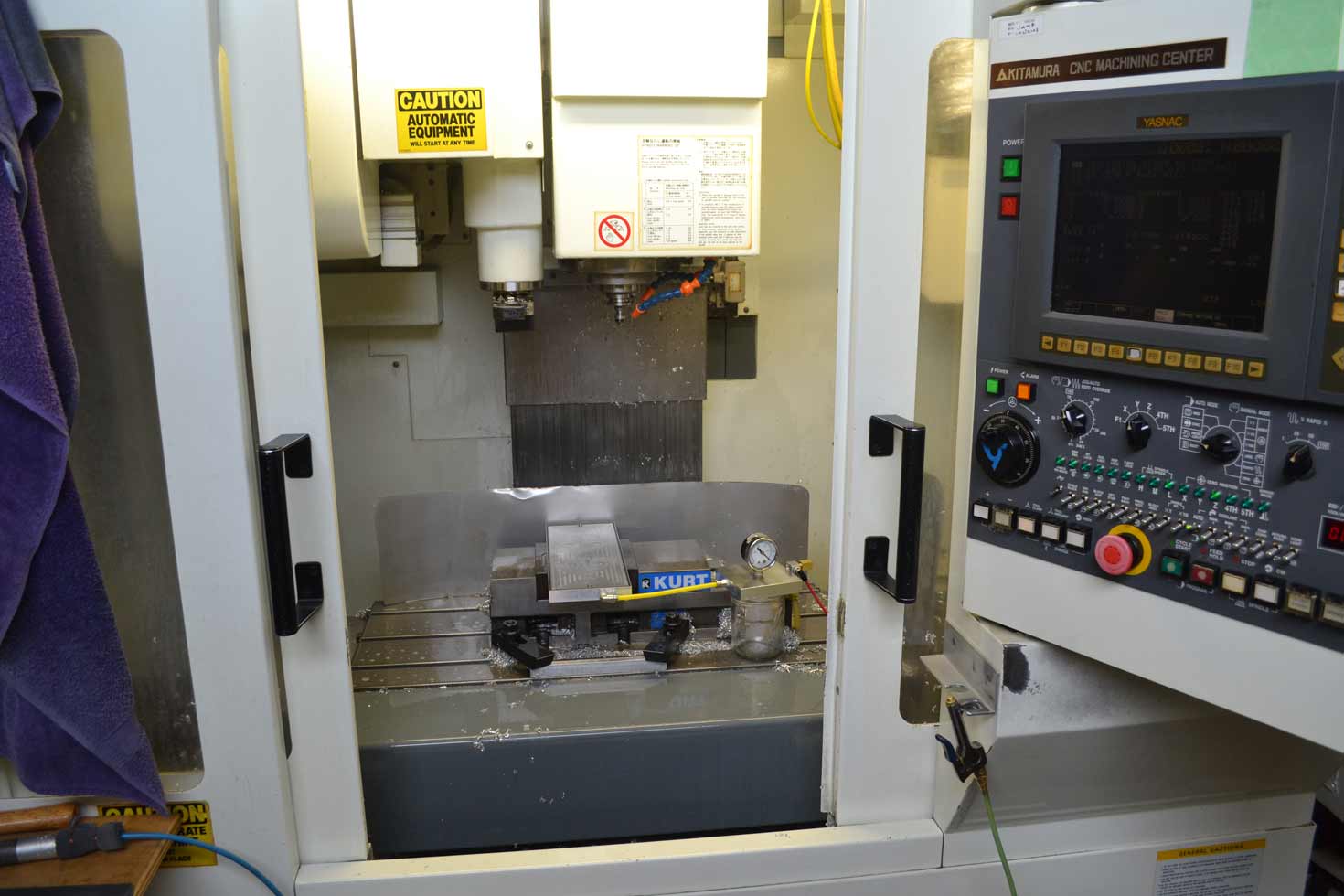
Last edited: