kuraki
Fimbulvetr Knifeworks
- Joined
- Jun 17, 2016
- Messages
- 4,679
Ok, I read the stickies. Read a number of searched threads. I'm now posting for some confirmation of assumptions or conclusions I've made from trying to collate all that information before I start buying components.
Goal: Two, independently controlled 220V heat treat furnaces with 8x8x22.5" chambers. When used separately, I'd like to use one for austenitizing and one for tempering. However, they're designed to join together end to end for a single 45" chamber that I could harden and temper sword length objects in.
Fabrication Plan:
14 gauge steel shell, K23 firebrick insulation with some wool to fill open corners. Bolted connections for putting both ovens end to end, as well as covers for using them independently. Welded/bent with exception of the top cover, so it can be removed for maintenance, brick replacement, etc.
Wiring components:
(2) PID controllers like this:
http://auberins.com/index.php?main_page=product_info&cPath=1&products_id=4
http://auberins.com/index.php?main_page=product_info&cPath=1&products_id=4
(4) SSRs like this:
http://www.auberins.com/index.php?main_page=product_info&cPath=2_30&products_id=30
(2) Thermocouples like this:
http://auberins.com/index.php?main_page=product_info&cPath=3&products_id=39
(Unsure yet of quantity) Heating elements like this:
http://www.budgetcastingsupply.com/product-p/7101-002.htm
Additional wiring components like fuses and signal wire, heavier wire, switches to wire up each of these unit like the following diagram:
Ok. Specific questions- How do I figure how much heating element for this setup? How do I route the elements to avoid running them along the rear wall, while also avoiding the need for additional circuits? Does this plan seem reasonable to those of you who have built your own furnace?
Goal: Two, independently controlled 220V heat treat furnaces with 8x8x22.5" chambers. When used separately, I'd like to use one for austenitizing and one for tempering. However, they're designed to join together end to end for a single 45" chamber that I could harden and temper sword length objects in.
Fabrication Plan:
14 gauge steel shell, K23 firebrick insulation with some wool to fill open corners. Bolted connections for putting both ovens end to end, as well as covers for using them independently. Welded/bent with exception of the top cover, so it can be removed for maintenance, brick replacement, etc.
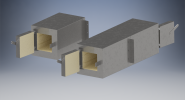
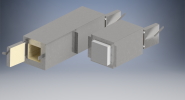
Wiring components:
(2) PID controllers like this:
http://auberins.com/index.php?main_page=product_info&cPath=1&products_id=4
http://auberins.com/index.php?main_page=product_info&cPath=1&products_id=4
(4) SSRs like this:
http://www.auberins.com/index.php?main_page=product_info&cPath=2_30&products_id=30
(2) Thermocouples like this:
http://auberins.com/index.php?main_page=product_info&cPath=3&products_id=39
(Unsure yet of quantity) Heating elements like this:
http://www.budgetcastingsupply.com/product-p/7101-002.htm
Additional wiring components like fuses and signal wire, heavier wire, switches to wire up each of these unit like the following diagram:
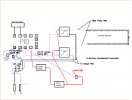
Ok. Specific questions- How do I figure how much heating element for this setup? How do I route the elements to avoid running them along the rear wall, while also avoiding the need for additional circuits? Does this plan seem reasonable to those of you who have built your own furnace?