Got a chance this morning to tour the blacksmith shop at the Nevada Northern Railway, in Ely, Nev. The entire railroad is on the National Register of Historic Places and now operated as a nonprofit. Many of the buildings exist in a kind of suspended animation, as if all the workers just stepped out for a smoke break.
Anyway, check out this gigantic steam-powered forging hammer. Wanna forge a REALLY BIG knife? Here's your tool:
Those gears on the wall in the background are actually wooden forms used for casting the real metal gears & wheels.
Rack of blacksmith tools:
The room next door is home to these two giant steam boilers, each is about 6' in diameter:
Next door to that is the main room of the machine shop. In one corner is this huge grinding/sharpening wheel, about 4' in diameter and still ready to work:
And here's one of several gigantic metalworking machines nearby, this one a horizontal lathe of some sort:
Thanks for tagging along!
Anyway, check out this gigantic steam-powered forging hammer. Wanna forge a REALLY BIG knife? Here's your tool:
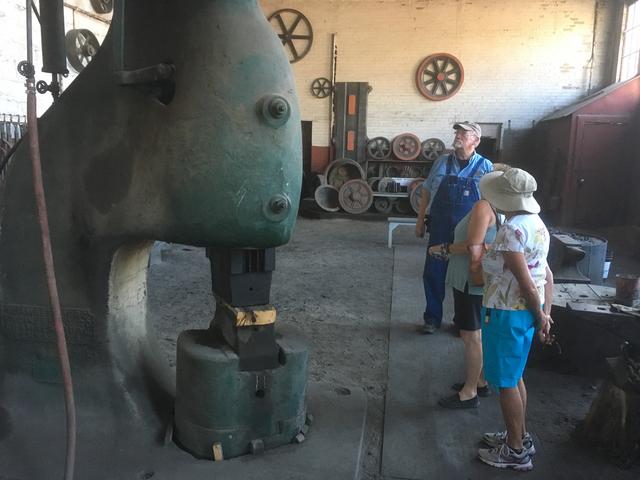
Those gears on the wall in the background are actually wooden forms used for casting the real metal gears & wheels.
Rack of blacksmith tools:
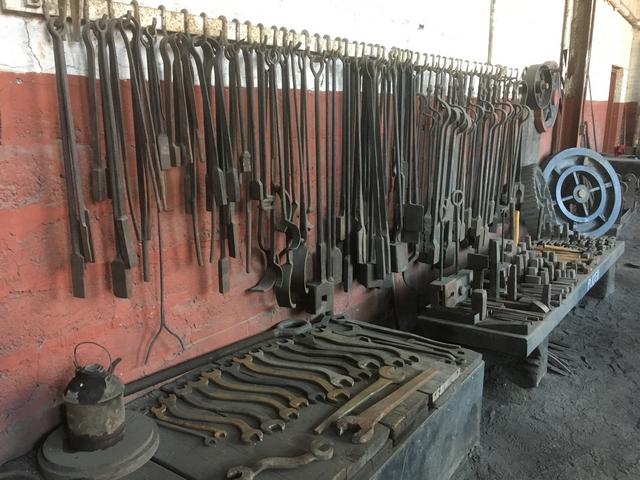
The room next door is home to these two giant steam boilers, each is about 6' in diameter:
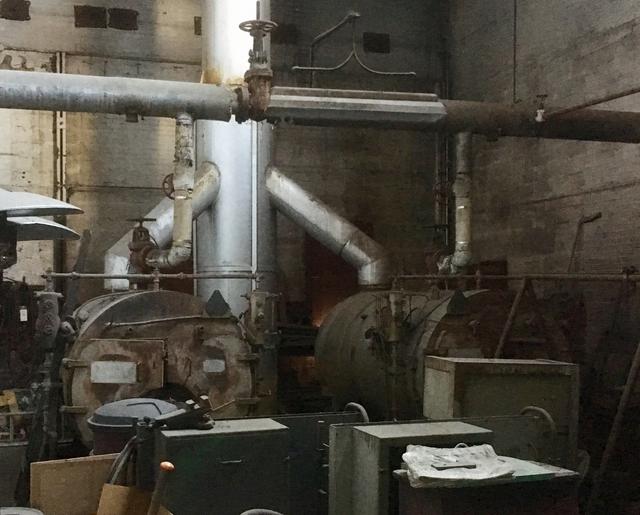
Next door to that is the main room of the machine shop. In one corner is this huge grinding/sharpening wheel, about 4' in diameter and still ready to work:
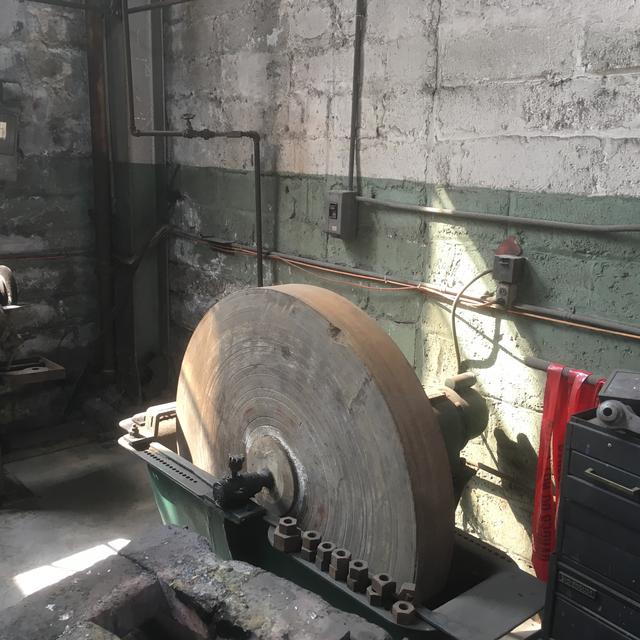
And here's one of several gigantic metalworking machines nearby, this one a horizontal lathe of some sort:

Thanks for tagging along!