I agree with Natlek -
Use a 1/4" to 3/8" thick piece of 1075 or 1084 for the bit and forge weld in the taco fashion. Fold the softer cladding steel in a "U" and insert the flat bit piece in the middle. Forge weld together. I leave about 1/2" to 3/4" empty space in the back of the taco to drift the eye later.
A good trick and a few tips are -
When the two pieces are snugly fitted, ground/filed clean, and ready to forge weld - clamp the bit/taco together tightly in a vise and run a MIG/TIG/stick bead down the top and bottom edge seams. After forge welding the bit in the cladding taco, open it up at full forging heat to create a roughly round eye. Use MIG/IG/stick to run a nice clean bead down the inside seams of the bit in the eye. Clean it up with a rotary file/burr or a round bastard file. This will assure that the bit doesn't start to separate when forging out the hawk/axe face and drifting the eye to shape. (If you are good at welding, you can weld all the seams initially and do a dry weld.)
Remember to drift the eye starting at a very hot temperature, close to welding heat.
Leave extra bit metal sticking out. Once you have forged the beard and tapers of the cheeks you can cut/grind it back and finish the edge bevel. Too much metal is much easier to fix than too little.
Work from side to side as you draw out the cheeks and eye. If one side ends up thicker than the other grind the excess away. You will likely create an oversize eye if you try to forge out the excess.
When working the cheeks, put the drift in the eye to keep it from turning sideways. Some folks who forge hawks and axe heads regularly make a special tong with a drift on one side and a forked piece on the other. This holds the head perfectly while drawing the shape out. You will definitely want to buy/make a simple tong with both ends turned inward to grip the eye.
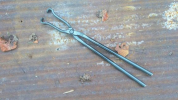