Occasionally the question comes up of making knives from already hardened steel. I figured I would show some of the steps I do when making knvies out of power hacksaw blades.
Years ago an older knife maker in Australia was kind enough to mentor me into my exploration of knives and steel. John was adamant that one of the best hardened steels for making knives out of is Starrett Redstripe HSS power hack saw blades. He contended the heat treat is on an industrial level so a good quality and since they are HSS they can take more heat when grinding which is a benefit.
The steel of the phbs is probably M2 or something similar so they do not grind like butter but for beginning sometimes slow grinding is a good thing as it is harder to make a major mistake.
At times you can find very good deals on phbs off of eBay. There are many different sizes and thicknesses of the blades, I would recomned finding a phb that is 0.075 inches thick so you have less material to remove.
Unfortunately my only phb left in the shop was 0.100.
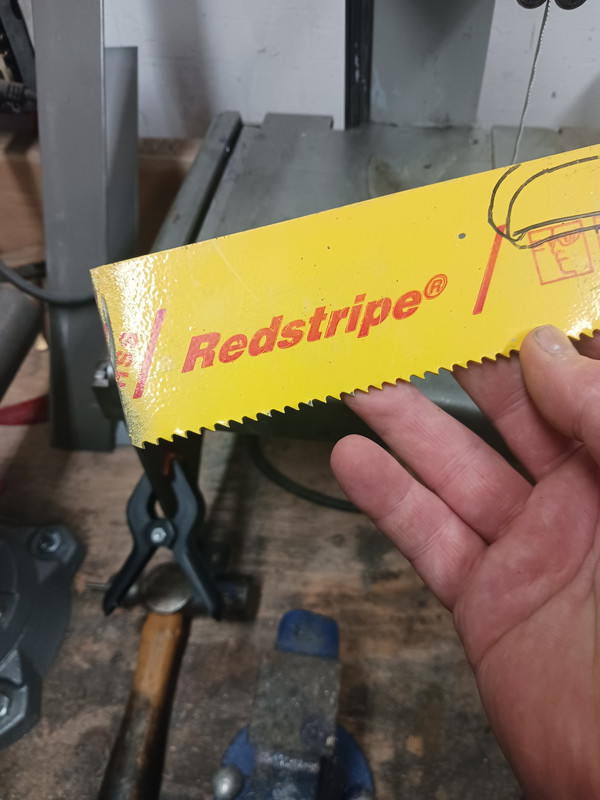
A cut off wheel on an angle grinder works well for rough cutting out your pattern. Be mindful of the heat created when cutting out the blank, cut wide of your pattern lines so you can clean up any haz on a grinder. Also be aware that cheap cutoff discs have been know to break in use so wear plenty of safety gear.
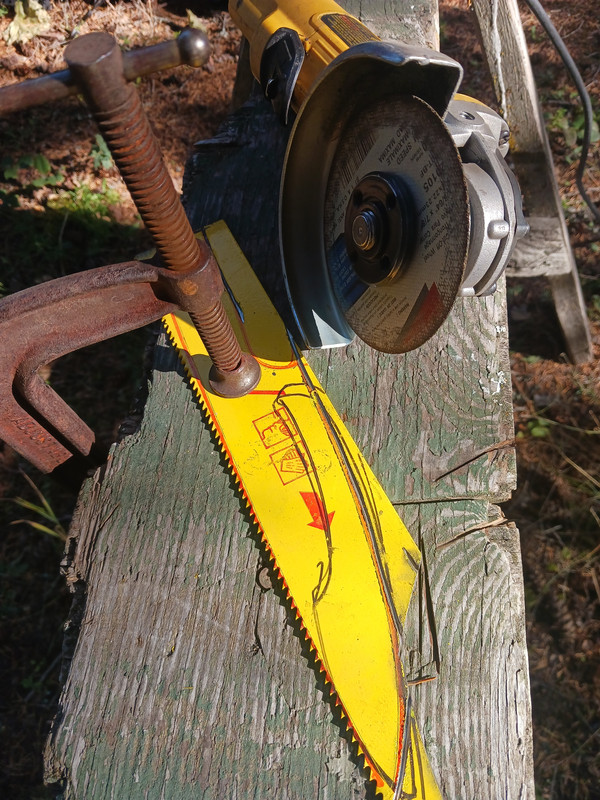
Rough cut and ready for shaping on the grinder.
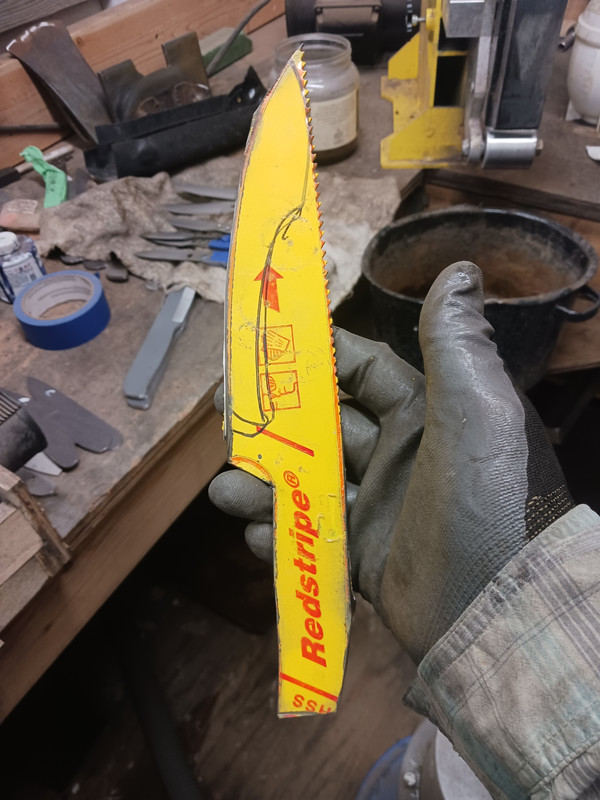
I was asked about hardness of the phbs so I surface ground and checked Rockewell. Yes they are hard, perfect for a slicing knife.
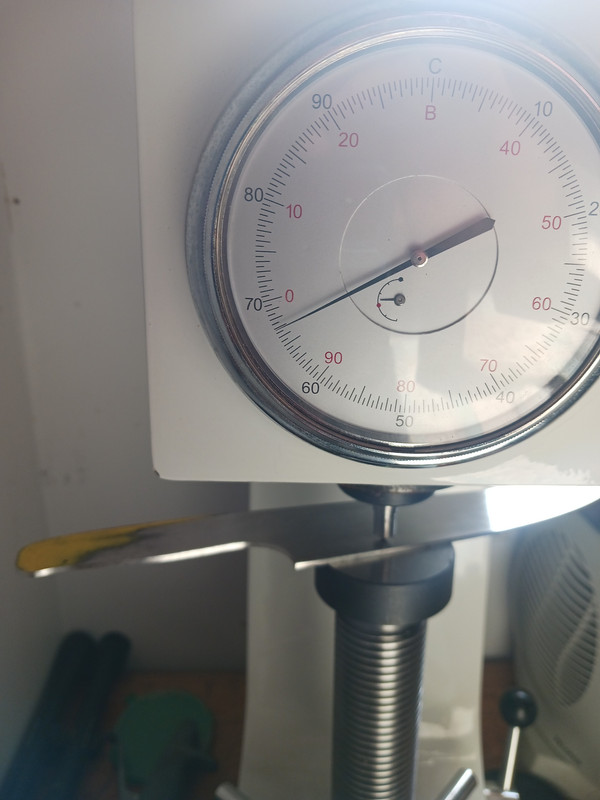
Now the fun part, tang holes.
I made a divot where I wanted the tang holes using a small dremel diamond bit.
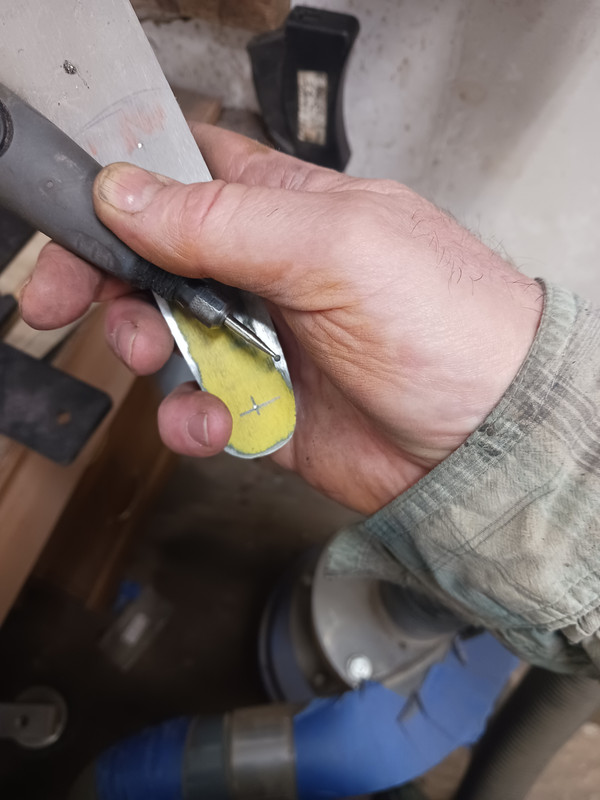
Then I use cheap Amazon tile and glass spade bits. I did destroy a couple of the bits in drilling the holes. Even when the bits start fracturing I keep applying pressure until the bits completely stop cutting.
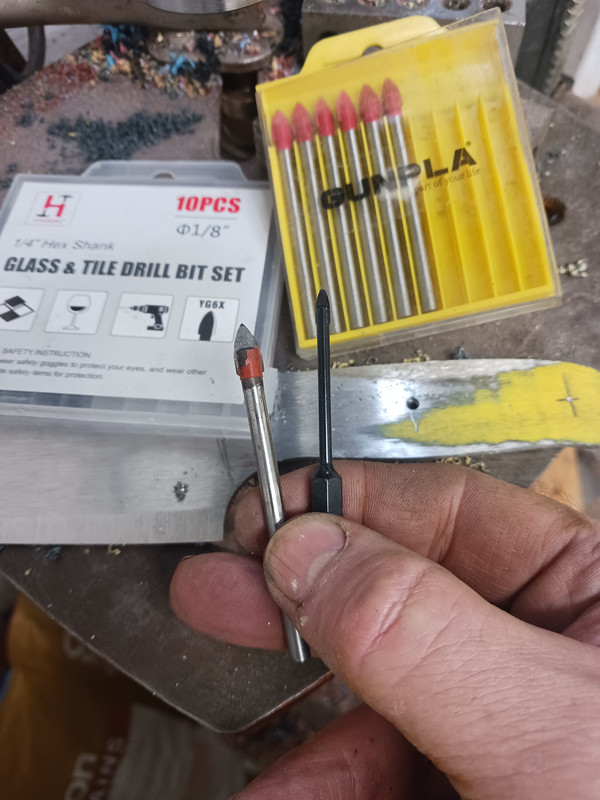
The 1/4 inch bits were not actually 1/4 so I used a carbdie tungsten burr to open up the holes.
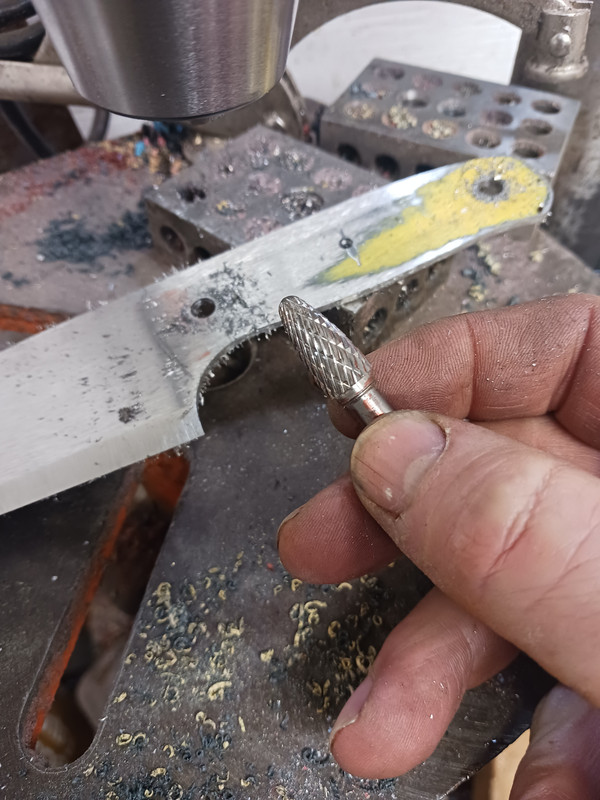
Good luck!
Years ago an older knife maker in Australia was kind enough to mentor me into my exploration of knives and steel. John was adamant that one of the best hardened steels for making knives out of is Starrett Redstripe HSS power hack saw blades. He contended the heat treat is on an industrial level so a good quality and since they are HSS they can take more heat when grinding which is a benefit.
The steel of the phbs is probably M2 or something similar so they do not grind like butter but for beginning sometimes slow grinding is a good thing as it is harder to make a major mistake.
At times you can find very good deals on phbs off of eBay. There are many different sizes and thicknesses of the blades, I would recomned finding a phb that is 0.075 inches thick so you have less material to remove.
Unfortunately my only phb left in the shop was 0.100.
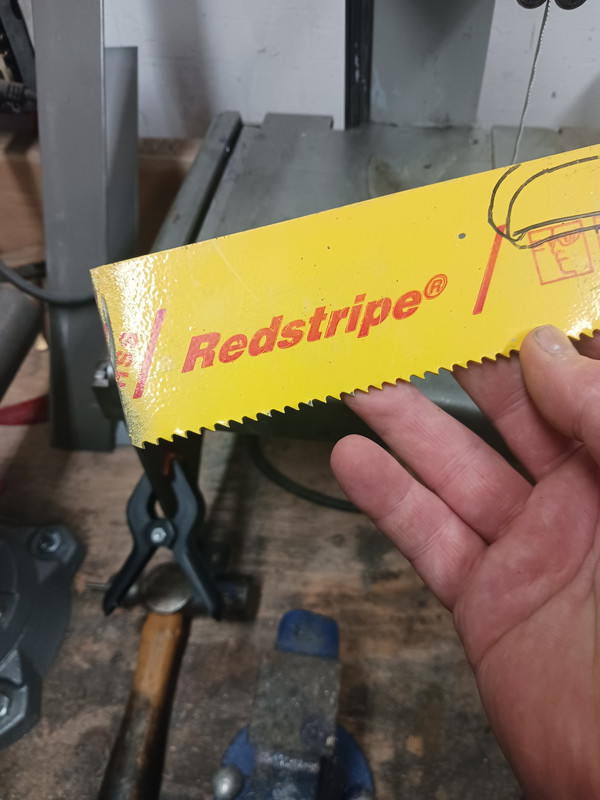
A cut off wheel on an angle grinder works well for rough cutting out your pattern. Be mindful of the heat created when cutting out the blank, cut wide of your pattern lines so you can clean up any haz on a grinder. Also be aware that cheap cutoff discs have been know to break in use so wear plenty of safety gear.
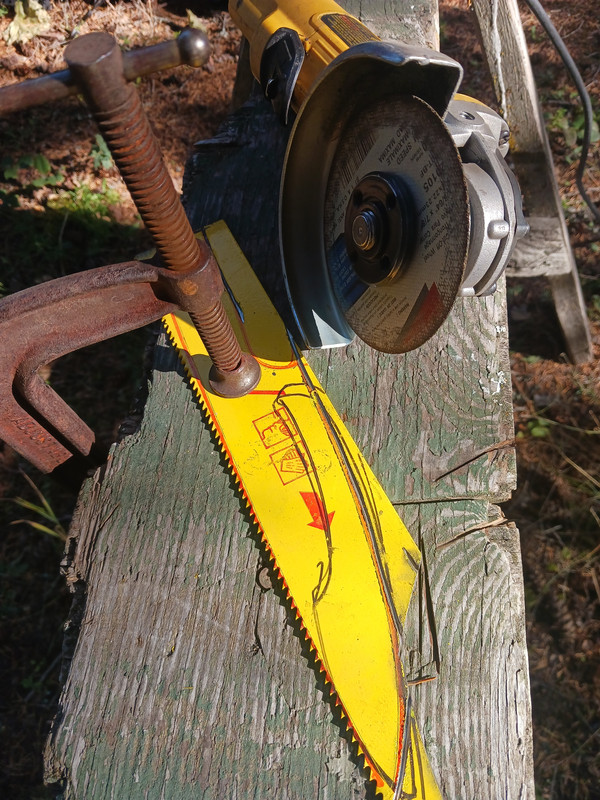
Rough cut and ready for shaping on the grinder.
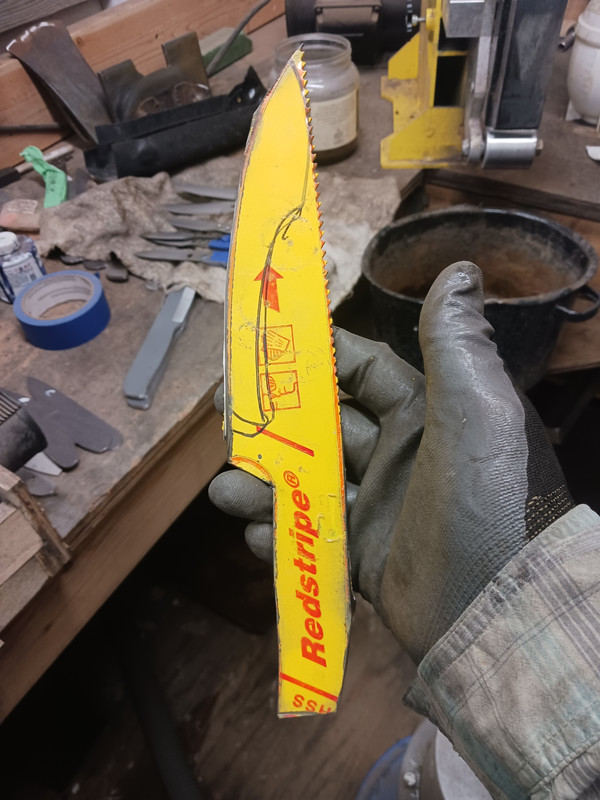
I was asked about hardness of the phbs so I surface ground and checked Rockewell. Yes they are hard, perfect for a slicing knife.
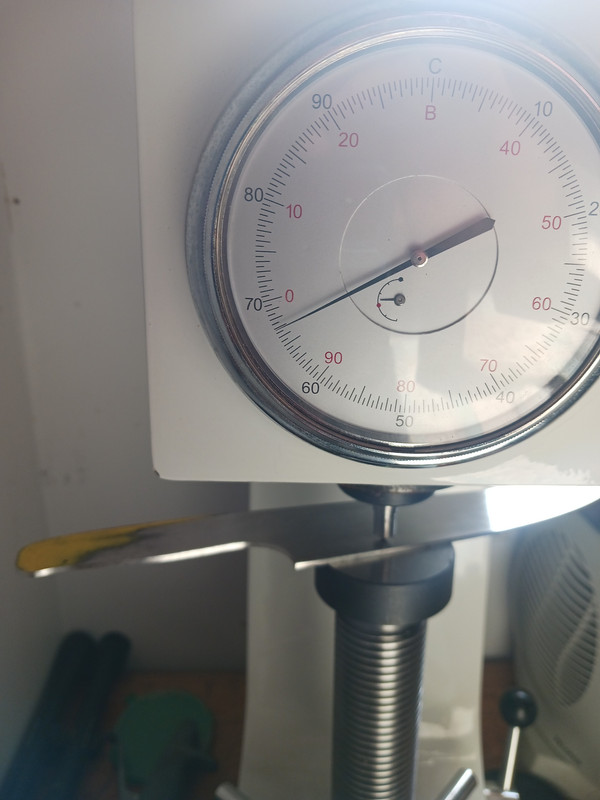
Now the fun part, tang holes.
I made a divot where I wanted the tang holes using a small dremel diamond bit.
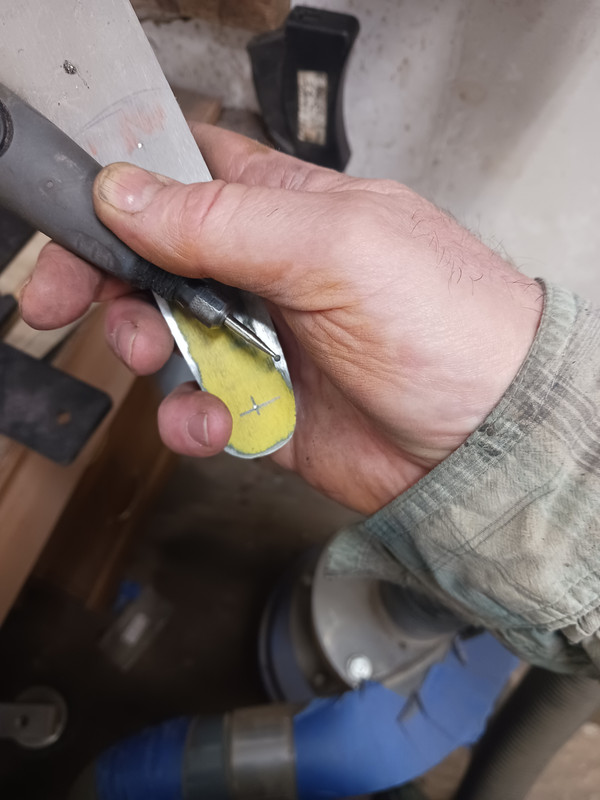
Then I use cheap Amazon tile and glass spade bits. I did destroy a couple of the bits in drilling the holes. Even when the bits start fracturing I keep applying pressure until the bits completely stop cutting.
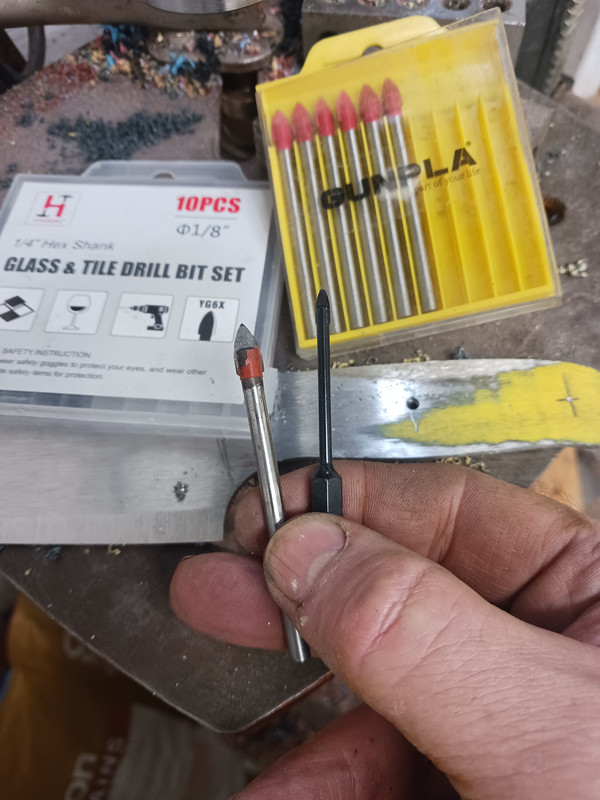
The 1/4 inch bits were not actually 1/4 so I used a carbdie tungsten burr to open up the holes.
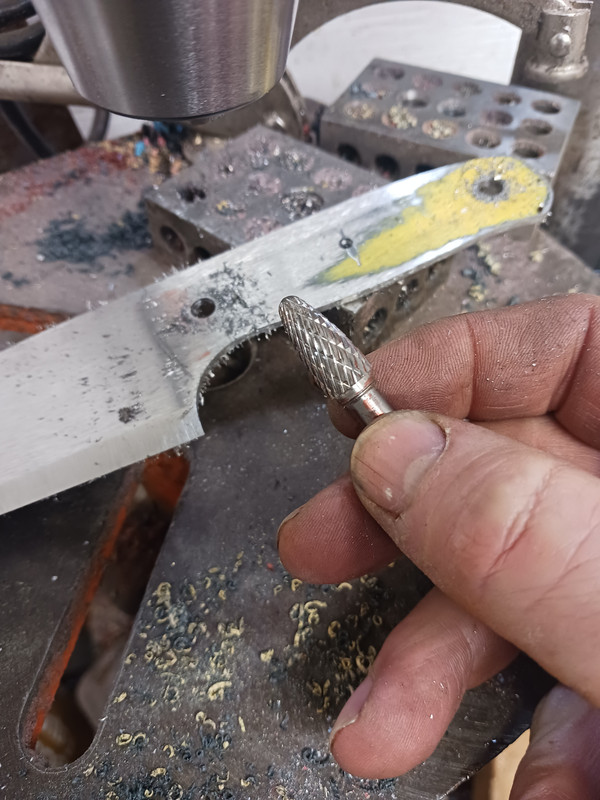
Good luck!