- Joined
- Sep 16, 2015
- Messages
- 157
Starts off with the heart of it all, the 50 ton cylinder:
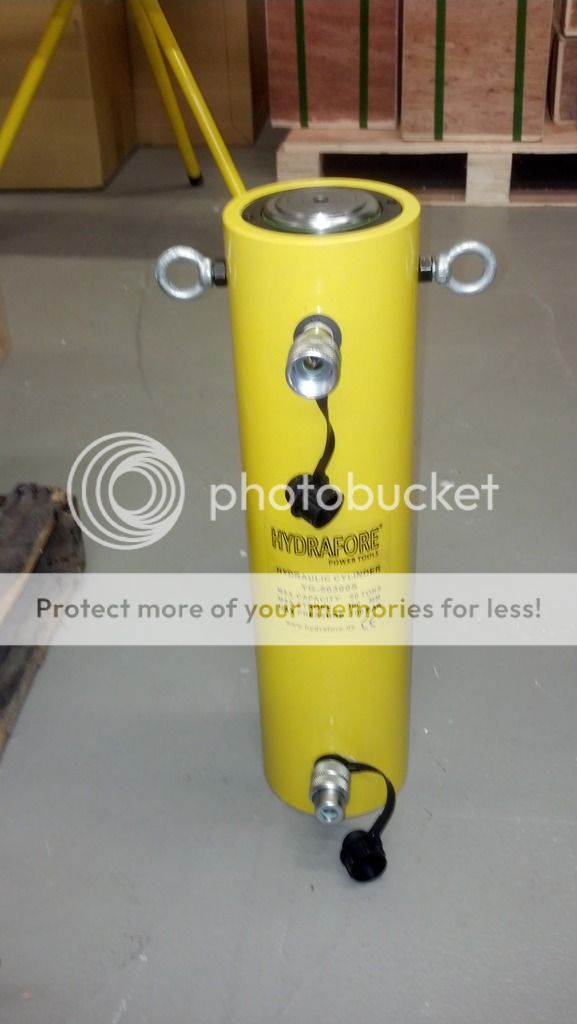
Then comes the frame:

Using 1x2x3 blocks to ensure alignment.
Built a cart for it to roll around on. 24x24:

Milled this pocket out of the 1" thick steel for the cylinder to sit in:

Also here is what is under the cylinder plate. Several 1x2" thick steel ribs:

Everything starting to come together:

Here is the hydraulic unit that powers the cylinder:

All self enclosed and protected in sheet metal.
Here is the unit fully assembled:


A view from the back:

Removable panels to service anything:

12" of travel:

the front and rear guards are reenforced with steel angle, so I can use them as short working tables:

PSI guage off to the side:

10,000 PSI @ 50 Tons.
Some of the dies:

And of course, the poorly edited videos:
[video=youtube_share;P-lF13Y-yUM]http://youtu.be/P-lF13Y-yUM[/video]
[video=youtube_share;-jyLZ9S2uNs]http://youtu.be/-jyLZ9S2uNs[/video]
[video=youtube_share;CGRL5gYseT8]http://youtu.be/CGRL5gYseT8[/video]
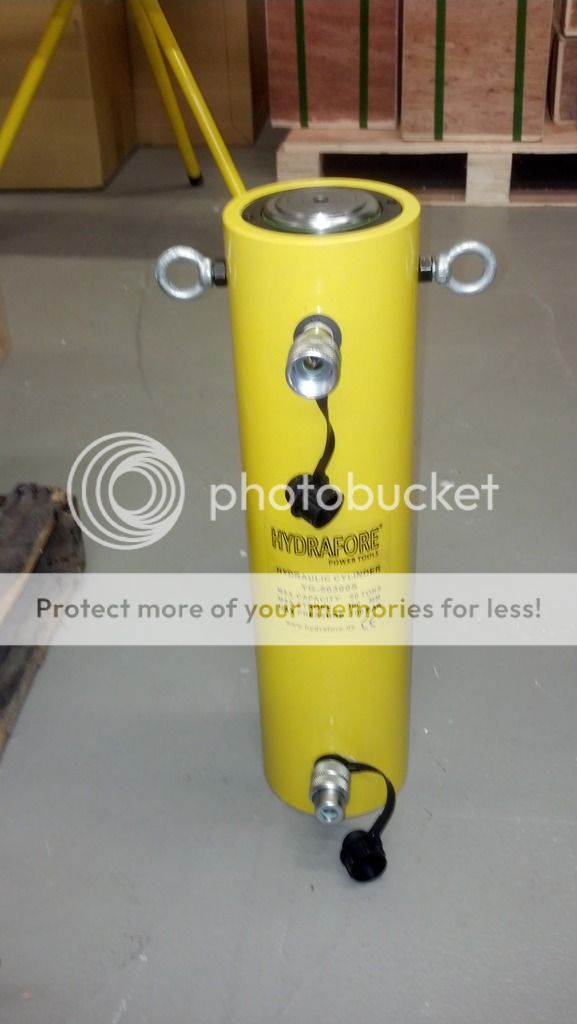
Then comes the frame:

Using 1x2x3 blocks to ensure alignment.
Built a cart for it to roll around on. 24x24:

Milled this pocket out of the 1" thick steel for the cylinder to sit in:

Also here is what is under the cylinder plate. Several 1x2" thick steel ribs:

Everything starting to come together:

Here is the hydraulic unit that powers the cylinder:

All self enclosed and protected in sheet metal.
Here is the unit fully assembled:


A view from the back:

Removable panels to service anything:

12" of travel:

the front and rear guards are reenforced with steel angle, so I can use them as short working tables:

PSI guage off to the side:

10,000 PSI @ 50 Tons.
Some of the dies:

And of course, the poorly edited videos:
[video=youtube_share;P-lF13Y-yUM]http://youtu.be/P-lF13Y-yUM[/video]
[video=youtube_share;-jyLZ9S2uNs]http://youtu.be/-jyLZ9S2uNs[/video]
[video=youtube_share;CGRL5gYseT8]http://youtu.be/CGRL5gYseT8[/video]