I have made a blank out of O2 tool steel and I hardened today on school.
Well I think I have hardened, I heated it up to a nice cherry red color and then quenched in the oil (which was a little warmed up).
It shows a nice black even finish but when I take a file and run it over the blade it still bites in the edges.
So my question is did I do it right?
I didn't do the magnet test.
And if it isn't good, can I just heat it back up to the good temp en quench it again? Or do I have the anneal it first?
Couple pics, you cant see it very good but it is in indication.
Grabt it on the handle and heated it half way te handle to the tip.
Well I think I have hardened, I heated it up to a nice cherry red color and then quenched in the oil (which was a little warmed up).
It shows a nice black even finish but when I take a file and run it over the blade it still bites in the edges.
So my question is did I do it right?
I didn't do the magnet test.
And if it isn't good, can I just heat it back up to the good temp en quench it again? Or do I have the anneal it first?
Couple pics, you cant see it very good but it is in indication.
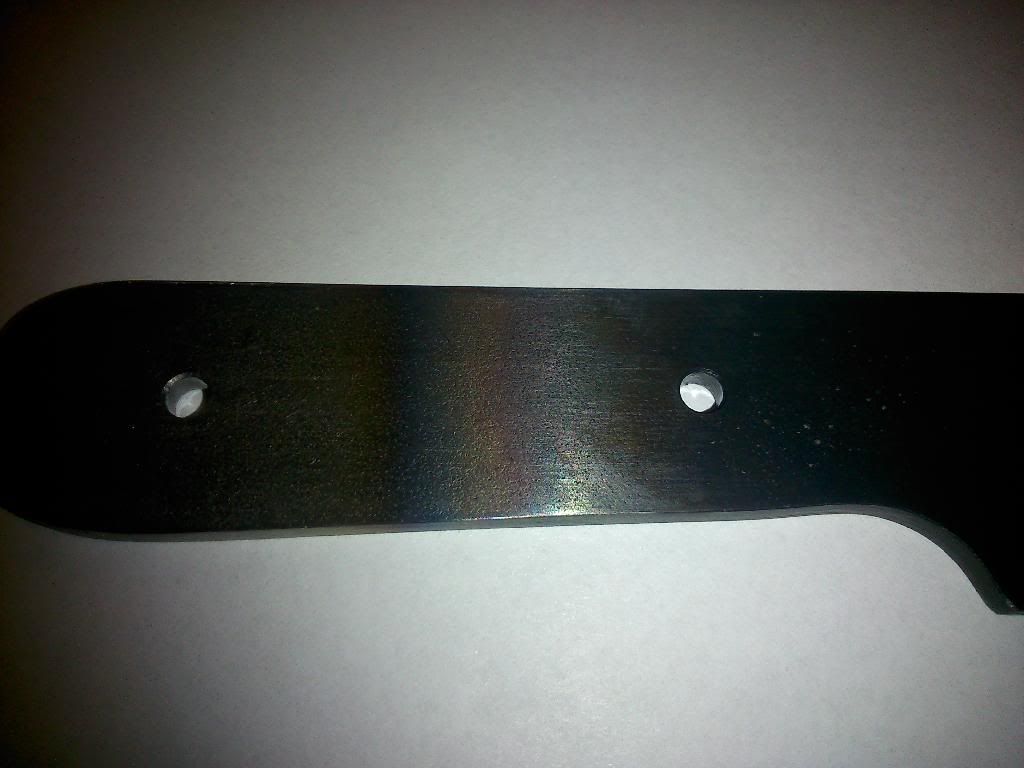
Grabt it on the handle and heated it half way te handle to the tip.
