Sean Yaw
Gold Member
- Joined
- Feb 26, 2019
- Messages
- 416
I finished my first peened together knife and have a couple questions. As you can see in the attached pictures, I managed to split the peened material (416 SS) at the edges which leaves an unsightly look, and likely compromised integrity of the joint. My naive logic leads me to suspect two possible culprits: (1) I made the counterbores too large, which forced me to try and expand the material too much and/or (2) I went too quickly and hit too hard and caused the splitting. I would appreciate any insight you would be willing to share.
My second question relates to process ordering. I finished the handles and then did the peening. The process of flattening the domed ends with a file and sandpaper led me to scratch everything up and just redo the handle finish. Should I just be more careful, or is it common to do handle finishing after peening is complete? Again, thank you so much for you feedback.

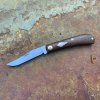
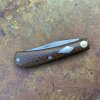
My second question relates to process ordering. I finished the handles and then did the peening. The process of flattening the domed ends with a file and sandpaper led me to scratch everything up and just redo the handle finish. Should I just be more careful, or is it common to do handle finishing after peening is complete? Again, thank you so much for you feedback.

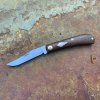
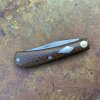