I will try to keep this to a reasonable length without going in a million directions and without giving too much background. So I am at risk of being misunderstood but otherwise it would be too long.
After forging the typical recommendation is normalizing. After forging there is often an uneven grain size, uneven distribution of stresses, and uneven distribution of cementite/carbides. Normalizing is at a relatively high temperature (1650-1700°F) to dissolve all of the carbides and to achieve an even (not necessarily smaller) grain size.
To achieve good grindability and for drilling holes, etc. An anneal is usually performed. There are several different types of anneals. Two important ones are a full cycle anneal (heat to austenite and slow cool) and another is a subcritical anneal where it is held below critical or cycled just below critical.
Grain refinement is not a required step and can be done at different stages. It is sometimes done after normalizing to refine the "new" grain structure and then a subcritical anneal is performed so that the prior austenite grain structure is not affected. It can also be done as part of final austenitization/hardening such as with a "prequench" or "triple quench." With grain refinement the purpose is to form small austenite grains, then cool to pearlite or martensite and then do it again. Therefore you want to be above critical to form austenite but too high would lead to larger grains which is not desirable for this step. So this step isn't required; many good knives have been made with steel that was forged, normalized, annealed, and then given a final heat treatment. But I know everyone wants their knives to be the best:
To add further complication there is also a "stress relief" treatment that can be done at even lower temperature (1100-1200°F) that is sometimes done after grinding operations to relieve stresses from grinding. It is essentially a high temperature tempering treatment.
A popular method of "thermal cycling" is to do a normalize followed by "grain refinement" cycles followed by a subcritical anneal. That leads to a decrease in temperature through these different cycle types: 1600-1700°F followed by 1350-1450°F followed by 1250-1300°F. Add a stress relief and you have even a fourth step at even lower temperature. So when you add that up you get this:
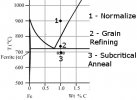
So someone saw that progression in temperature and decided if a little is good, then more is even better, and took the progression above which has some reason behind it and added in more steps in between:
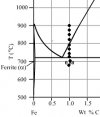
But for the reasons described above there isn't a purpose as far as I am aware to add in all of those temperatures in between.