- Joined
- Jun 5, 2012
- Messages
- 1,071
I'm editing this post in bit by bit, so please bear with me
I've gotten several requests for some info about my handle and blade finishing. I am going to try and do a start to finish soon, but these are some shots I snapped today for the interim.
The base platform for this knife is collectively my hidden tang hunters, which this is a variant of. I've boiled my style down to a handful of handle forms, and this is one. I don't claim to have "invented" this, I'm just showing my take on it.
Here's the parts, clean and ready for glue. I use G-Flex. Normally I run the tangs to 3/4 length if possible, but in this case the G10 is pretty heavy, and plenty strong, so I shorten the tang as much as reasonable for balance. This knife will still be incredibly strong.
First I start with the handle block straight and square, adjustments are made after gluing if necessary. DO NOT start sculpting before squaring and straightening the block to the blade. It will end badly. I draw the contours in primarily with French curves, sometimes using a flex curve, and circle and oval templates.
I remove the bulk of excess material on the bandsaw. If this was wood I probably would have removed more. G10 kills the blade so I try to keep the cuts to a minimum. I keep a blade specifically for composites, so that I don't ruin my others.
The first stage of this handle uses the flat platen on the 2x72, so I set it up, and I make sure my workrest is dead square. This is incredibly important on patterns such as this that have flats on the top and/or bottom, and reasonably important for others. Here I almost started grinding before I remembered I had set it to a negative angle when finishing the guard (to add a taper to the front of the handle).
On this material, I start with a fresh 100g j-flex, on low speed. Composites tend to heat when sanded, especially with worn belts. Worn belts are a bad idea in general with handle shaping, as they will give you unpredictable cutting depending on the pressure used and material. Some materials work decently with worn belts, softer ones such as redwood burl. 100 grit might be too aggressive on softer materials. In general I will start somewhere between 100g and 220g for initial shaping. Speed usually does not exceed 50%. Certain free cutting materials that don't burn easily can be run fast.
In this case, I am going to try and finish out the top and bottom as close to final as I can get, so I'm using smooth sweeping motions along the edges to gradually remove material. Do not try to hog off to the line. I normally only mark one side of the handle so I can see the profile unobstructed from the other side as I go. I don't always stick strictly to the lines, especially on a new pattern.
This is the roughing pass completed. After this I go 220, 320, 600, 1200. Your ability to skip grits will depend on the material and the belt wear. After I finish going around the edges up to 1200, the profile is completely finished and only the sides remain.
On a sculpted handle, it is VERY important to do each step sequentially and evenly. If you start trying to skip steps or finish one side first, it will only end in frustration, and a tremendous amount of extra work, possibly resulting in a failure to replicate the pattern. Here I put a flat taper on each side to match the guard. Notice the uneven areas around the top/bottom contours, and under the guard. Those can be finished with a small wheel attachment, or small drum sanding bits. The guard can be smoothed with cratex/rubberized abrasive points after the drum sanding bit.
Next I round the sides of the front half of the handle, following the taper I established on the previous step. I make sure to use reference points on the handle so that both sides are evenly contoured. This step shows 320g.
Next I start establishing the contour of the back half. This is a hollow area, so I switch to the 10" wheel. Having an assortment of wheel sizes is a huge help. 6, 8, 10 are all great sizes for bulk shaping. Small wheel attachments are also terrific. I do a similar thing here to the beginning of the front half, meaning that I just cut a straight scallop on each side, before starting to round and sculpt. I can't overstate the importance of working step by step on a handle like this. Marking guide lines isn't a bad idea either. This particular handle I can get away without, but in general guide marks are a good idea, even if just a centerline on the top, bottom, and sides.
After I have a flat scallop ground evenly on both sides, I start sculpting the curve. Once again I use fresh belts (usually one belt lasts 1-3 handles or so). First I sculpt the front half of the curve, as shown in this photo.
Once the front half is established on both sides, I sculpt in the back half. Then I sand up to 320g to match the front of the handle, and start walking up grits between the front and back of the handle. On this particular pattern, I need a clean break line between the front and back of the handle, so once I have the geometry well established, I'll move to the other half and start walking up the grits alternately between the front and back, so I keep my break in the proper place. Sorry for the blurry shot.
After I get up to 1200 grit on the entire handle, I hand sand the edges to soften. Then I will buff using a medium buff. The compound can vary, and sometimes I may buff without. Depends on the porosity and color of material. Some pieces may only be hand buffed, especially softer burls. IMO: Buffing is terrific for the "final touch" but SHOULD NOT be used to correct scratches caused by skipping grits, etc. The knife should already look nice once you go to the buffer. The buffer is just for that final bit of uniformity and soft character to the edges. Not all materials are suitable for buffing, and buffing will flat out ruin some stuff. This is trial and error. If you do choose to use a buffer. Be careful. Stay out of the way and think about what you are doing.
If all goes well, you should end up something like this:
Hope this was of some value to some folks. When I do the start to finish WIP on the other blade, I will elaborate on some of the specifics of how I finish wood.
I've gotten several requests for some info about my handle and blade finishing. I am going to try and do a start to finish soon, but these are some shots I snapped today for the interim.
The base platform for this knife is collectively my hidden tang hunters, which this is a variant of. I've boiled my style down to a handful of handle forms, and this is one. I don't claim to have "invented" this, I'm just showing my take on it.
Here's the parts, clean and ready for glue. I use G-Flex. Normally I run the tangs to 3/4 length if possible, but in this case the G10 is pretty heavy, and plenty strong, so I shorten the tang as much as reasonable for balance. This knife will still be incredibly strong.

First I start with the handle block straight and square, adjustments are made after gluing if necessary. DO NOT start sculpting before squaring and straightening the block to the blade. It will end badly. I draw the contours in primarily with French curves, sometimes using a flex curve, and circle and oval templates.

I remove the bulk of excess material on the bandsaw. If this was wood I probably would have removed more. G10 kills the blade so I try to keep the cuts to a minimum. I keep a blade specifically for composites, so that I don't ruin my others.

The first stage of this handle uses the flat platen on the 2x72, so I set it up, and I make sure my workrest is dead square. This is incredibly important on patterns such as this that have flats on the top and/or bottom, and reasonably important for others. Here I almost started grinding before I remembered I had set it to a negative angle when finishing the guard (to add a taper to the front of the handle).

On this material, I start with a fresh 100g j-flex, on low speed. Composites tend to heat when sanded, especially with worn belts. Worn belts are a bad idea in general with handle shaping, as they will give you unpredictable cutting depending on the pressure used and material. Some materials work decently with worn belts, softer ones such as redwood burl. 100 grit might be too aggressive on softer materials. In general I will start somewhere between 100g and 220g for initial shaping. Speed usually does not exceed 50%. Certain free cutting materials that don't burn easily can be run fast.

In this case, I am going to try and finish out the top and bottom as close to final as I can get, so I'm using smooth sweeping motions along the edges to gradually remove material. Do not try to hog off to the line. I normally only mark one side of the handle so I can see the profile unobstructed from the other side as I go. I don't always stick strictly to the lines, especially on a new pattern.

This is the roughing pass completed. After this I go 220, 320, 600, 1200. Your ability to skip grits will depend on the material and the belt wear. After I finish going around the edges up to 1200, the profile is completely finished and only the sides remain.

On a sculpted handle, it is VERY important to do each step sequentially and evenly. If you start trying to skip steps or finish one side first, it will only end in frustration, and a tremendous amount of extra work, possibly resulting in a failure to replicate the pattern. Here I put a flat taper on each side to match the guard. Notice the uneven areas around the top/bottom contours, and under the guard. Those can be finished with a small wheel attachment, or small drum sanding bits. The guard can be smoothed with cratex/rubberized abrasive points after the drum sanding bit.

Next I round the sides of the front half of the handle, following the taper I established on the previous step. I make sure to use reference points on the handle so that both sides are evenly contoured. This step shows 320g.

Next I start establishing the contour of the back half. This is a hollow area, so I switch to the 10" wheel. Having an assortment of wheel sizes is a huge help. 6, 8, 10 are all great sizes for bulk shaping. Small wheel attachments are also terrific. I do a similar thing here to the beginning of the front half, meaning that I just cut a straight scallop on each side, before starting to round and sculpt. I can't overstate the importance of working step by step on a handle like this. Marking guide lines isn't a bad idea either. This particular handle I can get away without, but in general guide marks are a good idea, even if just a centerline on the top, bottom, and sides.

After I have a flat scallop ground evenly on both sides, I start sculpting the curve. Once again I use fresh belts (usually one belt lasts 1-3 handles or so). First I sculpt the front half of the curve, as shown in this photo.

Once the front half is established on both sides, I sculpt in the back half. Then I sand up to 320g to match the front of the handle, and start walking up grits between the front and back of the handle. On this particular pattern, I need a clean break line between the front and back of the handle, so once I have the geometry well established, I'll move to the other half and start walking up the grits alternately between the front and back, so I keep my break in the proper place. Sorry for the blurry shot.

After I get up to 1200 grit on the entire handle, I hand sand the edges to soften. Then I will buff using a medium buff. The compound can vary, and sometimes I may buff without. Depends on the porosity and color of material. Some pieces may only be hand buffed, especially softer burls. IMO: Buffing is terrific for the "final touch" but SHOULD NOT be used to correct scratches caused by skipping grits, etc. The knife should already look nice once you go to the buffer. The buffer is just for that final bit of uniformity and soft character to the edges. Not all materials are suitable for buffing, and buffing will flat out ruin some stuff. This is trial and error. If you do choose to use a buffer. Be careful. Stay out of the way and think about what you are doing.
If all goes well, you should end up something like this:
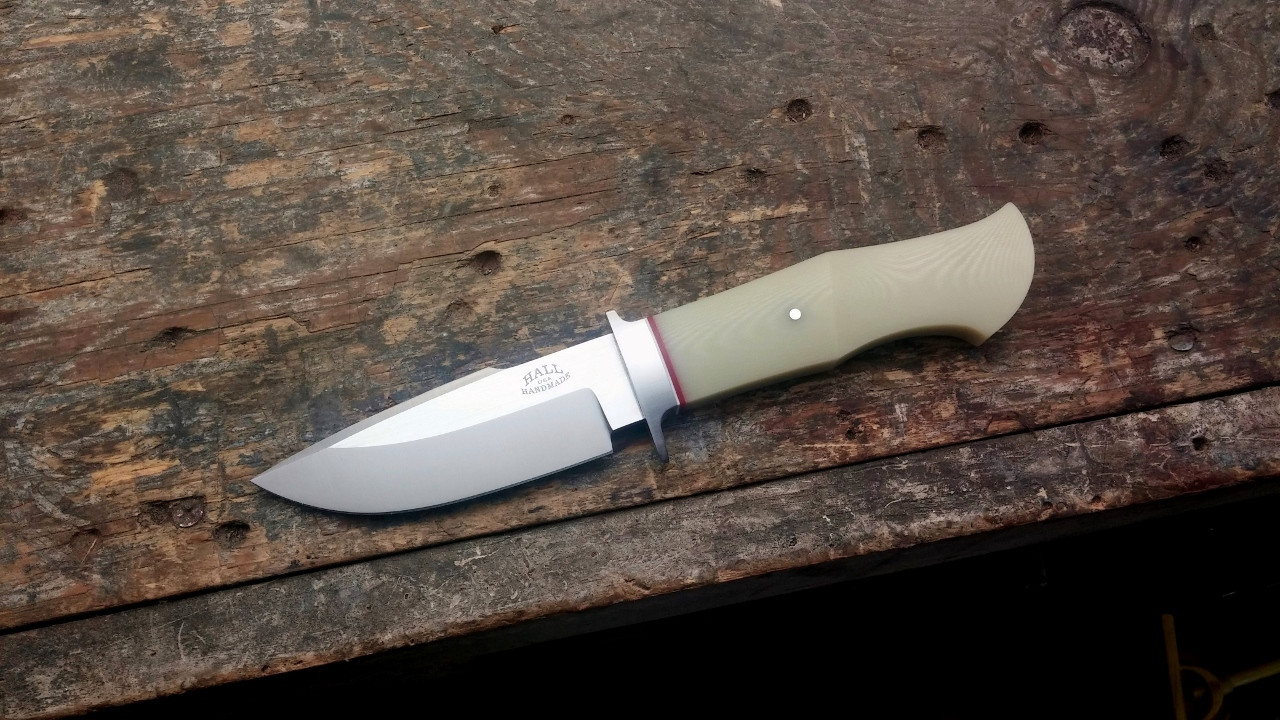
Hope this was of some value to some folks. When I do the start to finish WIP on the other blade, I will elaborate on some of the specifics of how I finish wood.
Last edited: