Francisco Vaz
fvazknives.com
- Joined
- Nov 10, 2017
- Messages
- 284
Hey guys, going straight to the point im having problems with mostly maple. Since my handle work is mostly done using 3/8" scales (around 9mm) they are "randomly" warping.
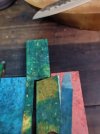
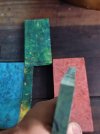
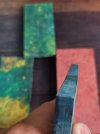
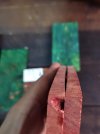
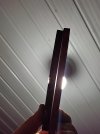
It seems they are getting worse each day. About 1 month ago they werent this bad, mostly was flat, now they are warping each time more.
Does this means any mistake during stabilization or is this natural? I really thought stabilized woods were meant to be "stable" under most climates and not meant to warp like this.
Im really upset as i bought a big ammount of stabilized woods and now everytime i want to use them i must handpick the very few that didnt warped. Very frustrating.
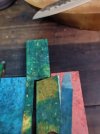
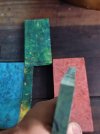
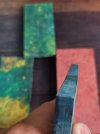
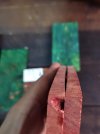
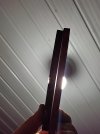
It seems they are getting worse each day. About 1 month ago they werent this bad, mostly was flat, now they are warping each time more.
Does this means any mistake during stabilization or is this natural? I really thought stabilized woods were meant to be "stable" under most climates and not meant to warp like this.
Im really upset as i bought a big ammount of stabilized woods and now everytime i want to use them i must handpick the very few that didnt warped. Very frustrating.