Holemaking is both overlooked and over analyzed often. Precision holes that conform to size, position, orientation, and form take more processing than holes that exist simply to create a pathway through another object. If you're making full tang, fixed blade knives and wish to drill holes for weight relief, glue wells, and clearance for pins, your needs are vastly different than those for someone who makes flipper folders for example. What the tariffs have to do with the drill press market, I don't know. Industrial quality drill presses are practically given away at surplus equipment auctions. The drill press simply doesn't have as much place in a modern job shop that it once did. It's still useful, it's still ideal to have one or two, but no longer do shops keep scores of them set up with drill jigs for production.
I got this double Buffalo drill table for $210. These are 3 phase, commercial drills on a blanchard ground cast iron table. They have a speed range of 460 to 3600 RPM. They're adjustable in height, have quill locks, and tapered spindles. They may not be ideal for someone else, but they're set up perfectly for me, as I wanted to be able to set up 2 presses for multiple operations (drill -> ream, or ream -> cbore, etc). While they're not set up in a way to make tramming easy, they can be trammed by shimming the pedestals, and I find that preferable to something meant to move, because they will stay where I put them.
This Powermatic is another auction buy. I think I paid $150 for this. It's also a commercial machine, though on the lower end of that scale. It has a JT33 taper spindle, and a huge size range. It also goes down to 400 RPM, I forget the top range. It has a little more spindle run out than the Buffalos do, so I don't use it for precision holes, but it is great for long drills in handle blocks, or running my tapping head.
I highly recommend perusing industrial auctions for any machine tools like drill presses or surface grinders. Those in particular, at least in my area, go quite inexpensively compared to their value to a knifemaker. The industrial bidders don't generally want them, and the personal buyers wouldn't know what to do with a surface grinder. Bandsaws and knee mills go for often more than I think they're worth, because theirs more market for them, but deals can be had on them too. Sometimes you'll have to fix or repair something, but to me that's worth the effort to have a commercial piece of equipment that's A) made to be repairable and B) vastly superior to homeowner market equipment.
If money were no object or if I'd found them at auction, the best drill presses I've ever worked with professionally were South Bend Ibarmia presses (geared head, fantastic speed ranges for metal work, excellent depth control) like this:
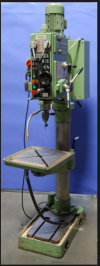
I missed out on one just like this for about $300.
And Solberga for similar reasons:
Just throwing that out there in case someone sees one of these at auction for a reasonable price. None of us would pay for a brand new one.
Generally though, I think having a reasonable quality drill and a milling machine for more precision holes is ideal for most people, or if you only have room for one, just a mill. The only thing a drill press has over a mill is size range for price and being generally faster to set up.