- Joined
- Feb 6, 2010
- Messages
- 1,427
I like bolsters on many of my knives and I experiment with odd shapes, rounded fronts, dovetails,etc. but the most problematic part for most newer knife makers is pinning the bolsters to the tang. When I started I used the method of Stephen R. Johnson using a nail set tool to form a chamfered hole on the bolsters by smacking the nail set into the holes drilled for the pins. This worked OK but did not provide a very strong grip and lost it's effectiveness rapidly if the bolster was ground down very much in finishing. I discovered a longer tapered chamfer tool for sale in either Jantz knife supply or Texas knife supply which worked well as long as the bolsters were well secured in a smallish vise designed to fit on top of a drill table. I used a couple scraps of leather to hold the bolsters in place to prevent marring. I ran the chamfer in about 3/32 or 1/8 of an inch deep which provides a secure grip and ended the "dreaded ghost ring of the pin" problem. The next problem to occur was the "Too tight to go through" problem. I thought I had this problem solved by using an oversized drill like a number 21 drill instead of a 5/32 drill for 5/32 pin stock. Well, the pins went in easily but were hard to set firmly and again resulted in the "ghost ring" problem. Now, I use the oversize drill for the tang holes but the regular drill for the bolster holes and make the pins a snug fit by sanding them lightly on a 400 grit belt by spinning the pin stock between my fingers while holding it to the belt. This is done by trial and error until the pins barely start to slide into the bolster holes and have to be tapped home with a small hammer. Now the part that some knife makers dread is peening the pin into place. The trick here in my opinion is to have about an 1/8 inch of pin standing above the holes on both sides of the bolsters and start them by hammering lightly with repeated taps of the flat face of a ball peen hammer. I ground the face of my 1 pound hammer flat with a disc sander. When the pins are flattened a bit then I use a 2 pound ball peen hammer with the peen side to shape the pins into the chamfered holes until they are about twice the diameter. They can be ground down on the disc sander to level. Having larger holes in the tang lets the pins expand without pulling the bolsters up. I used to pin my bolsters with smaller pin stock but now like 5/32 or even 3/16 stock to make a stronger knife. I sand the insides of the bolsters to 400 grit so the resulting fit is so tight that no joint can be seen (almost) . If any of you have a better method please comment. This is what works for me and may be of value to some of you. Larry
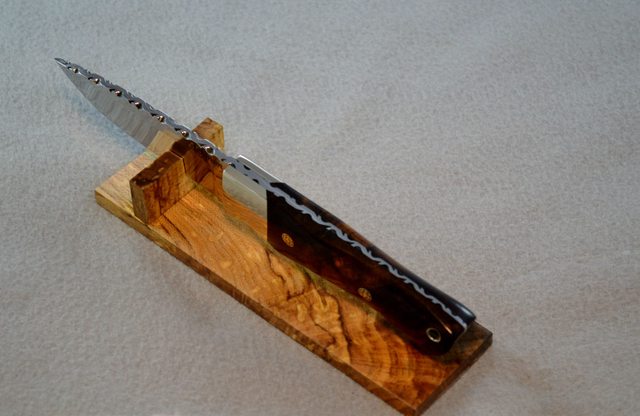