Larrin
Knifemaker / Craftsman / Service Provider
- Joined
- Jan 17, 2004
- Messages
- 4,970
Corrosion resistance of tool steels isn't studied much since they aren't designed for corrosive environments. However, knife makers are often interested in the relative corrosion resistance of these steels as there can be benefits to offering "some" corrosion resistance while also offering superior performance to stainless steels. Many knifemakers have advertised their D2 knives as being "semi-stainless." However, with the lack of information available, how does one know which tool steels are likely to offer better corrosion resistance? The "bulk" chromium content of the steel is not necessarily a good indicator because some of that chromium is usually tied up in chromium carbides.
Using thermodynamic calculations along with an austenitizing temperature, we can calculate a predicted amount of chromium in solution, which is a good indicator for relative corrosion resistance. The more chromium there is in solution, the more complete will be the passive film of chromium oxide that contributes to stain resistance, as shown below:
Another measure of corrosion resistance is pitting resistance, which is calculated with this equation:
PREN = Cr% + 3.3*(Mo%+0.5*W%) + 16*N%
However this equation can be somewhat misleading because molybdenum, for example, helps with pitting because it helps where the passive film breaks down, not by creating its own passive film. Crucible metallurgists used this equation after experience with 154CM (4% Mo) to design S30V and S110V with intentional additions of Mo. However, if the chromium oxide film isn't mostly complete no amount of molybdenum is going to make up for it. After all, we don't have any moly-only stainless steels. Therefore, in this case where these tool steels all have less than 10% Cr in solution, I think looking at chromium content in solution is most useful when predicting stain resistance.
Here is the chromium in solution I calculated, along with two stainless steels for comparison at the top:
As you can see, D2 does not have the highest chromium in solution! While A8 mod (chipper knife steel) is less commonly used, 3V is certainly pretty common, and it is predicted to have significantly more chromium in solution than D2. Another interesting note is that most of the chromium in 52100 is in solution rather than being tied by carbides, which is perhaps expected by its relatively low bulk chromium content. One potential caveat: if any of these steels are heat treated with an upper temper, a significant amount of chromium will be precipitated out as carbides reducing the corrosion resistance, which is why datasheets for stainless steels always say use the lower temper for best stain resistance. Therefore, 3V might only be superior to D2 if using a lower temper.
Using thermodynamic calculations along with an austenitizing temperature, we can calculate a predicted amount of chromium in solution, which is a good indicator for relative corrosion resistance. The more chromium there is in solution, the more complete will be the passive film of chromium oxide that contributes to stain resistance, as shown below:
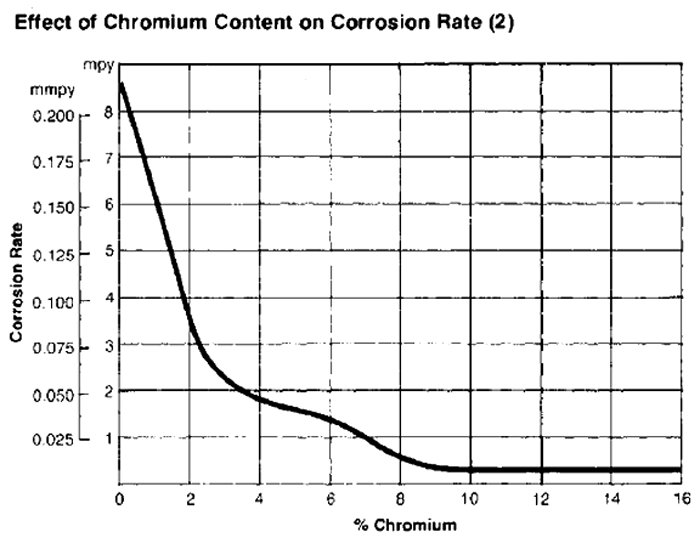
Another measure of corrosion resistance is pitting resistance, which is calculated with this equation:
PREN = Cr% + 3.3*(Mo%+0.5*W%) + 16*N%
However this equation can be somewhat misleading because molybdenum, for example, helps with pitting because it helps where the passive film breaks down, not by creating its own passive film. Crucible metallurgists used this equation after experience with 154CM (4% Mo) to design S30V and S110V with intentional additions of Mo. However, if the chromium oxide film isn't mostly complete no amount of molybdenum is going to make up for it. After all, we don't have any moly-only stainless steels. Therefore, in this case where these tool steels all have less than 10% Cr in solution, I think looking at chromium content in solution is most useful when predicting stain resistance.
Here is the chromium in solution I calculated, along with two stainless steels for comparison at the top:

As you can see, D2 does not have the highest chromium in solution! While A8 mod (chipper knife steel) is less commonly used, 3V is certainly pretty common, and it is predicted to have significantly more chromium in solution than D2. Another interesting note is that most of the chromium in 52100 is in solution rather than being tied by carbides, which is perhaps expected by its relatively low bulk chromium content. One potential caveat: if any of these steels are heat treated with an upper temper, a significant amount of chromium will be precipitated out as carbides reducing the corrosion resistance, which is why datasheets for stainless steels always say use the lower temper for best stain resistance. Therefore, 3V might only be superior to D2 if using a lower temper.
Last edited: