Another welding session done. Drew out the sr and sky, and finished the re-stacks of the can and the fittings billet. Will restack the fittings one more time.
I leveled out the billets with a kiss block that was about .7. Then I put them on the SH attachment and ground the flats clean enough to lay them out. Quick etch to check the patterns. Next I’ll anneal then start the final weld prep. All the “easy” parts are done, all difficult from here.
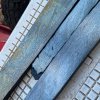
I leveled out the billets with a kiss block that was about .7. Then I put them on the SH attachment and ground the flats clean enough to lay them out. Quick etch to check the patterns. Next I’ll anneal then start the final weld prep. All the “easy” parts are done, all difficult from here.
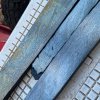