- Joined
- Mar 25, 2014
- Messages
- 2,010
The molten Babbitt flowed through the holes we drilled a while ago. The metal cooled down and solidified when it met the surfaces of the barrel. This is how the "rivet" heads were formed and what holds this chevron nose cap in position.
But, my faith was well founded and perseverance was the ticket. Actually, I'd call it more like "the Labors of Hercules". But soon, I could start making out the pattern in the wood. Rasping was done carefully so as to not bugger up the wood and need to do some re-shaping. Still, I kept rasping away and made sure the contours of the wood were followed carefully so as to stay in perspective. It is extremely important that you do not remove too much material or the design will be filed away. Easy does it. Use different files and various grit sand papers to dress the inlay up and soon, stripes galore! The Sun shines on Corn Patch again.
The rifle was assembled and the fit of the components checked. Tweaking as necessary until I was satisfied. and here is the finished nose cap.
When pouring nose caps or inlays, they can be as simple or complex as you desire PROVIDING metal can get into the cavities you create. 3-D is also possible. Let your imagination run wild. Experiment on pieces of scrap hard wood. If you have the space or room, why settle for a simple Yin/Yang when you can pour an entire winged dragon whose tail wraps around the handle? Need a bolster for that Khuk? Here you go.
Remember that pouring metal inlays is not always a "given". Mother nature can and does create situations you do not want to deal with. Impurities can appear during filing that are too large to completely be removed. There is such an irregularity in the last photo. There is a little dent/hole/ imperfection on the top bar of the nose cap. In this case, I've cleaned it up and will leave it. After all, it's hand made and not store bought. Air pockets or voids will also appear every once in a while. This is usually caused from the molten metal from cooling down too rapidly and the air which is forced out of the cavity gets trapped. Some times you can do a tiny re-pour. This can be scary and quite dangerous. Safety first!
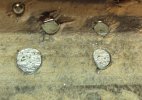
But, my faith was well founded and perseverance was the ticket. Actually, I'd call it more like "the Labors of Hercules". But soon, I could start making out the pattern in the wood. Rasping was done carefully so as to not bugger up the wood and need to do some re-shaping. Still, I kept rasping away and made sure the contours of the wood were followed carefully so as to stay in perspective. It is extremely important that you do not remove too much material or the design will be filed away. Easy does it. Use different files and various grit sand papers to dress the inlay up and soon, stripes galore! The Sun shines on Corn Patch again.
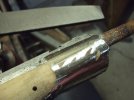
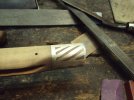
The rifle was assembled and the fit of the components checked. Tweaking as necessary until I was satisfied. and here is the finished nose cap.
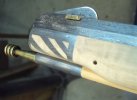
When pouring nose caps or inlays, they can be as simple or complex as you desire PROVIDING metal can get into the cavities you create. 3-D is also possible. Let your imagination run wild. Experiment on pieces of scrap hard wood. If you have the space or room, why settle for a simple Yin/Yang when you can pour an entire winged dragon whose tail wraps around the handle? Need a bolster for that Khuk? Here you go.
Remember that pouring metal inlays is not always a "given". Mother nature can and does create situations you do not want to deal with. Impurities can appear during filing that are too large to completely be removed. There is such an irregularity in the last photo. There is a little dent/hole/ imperfection on the top bar of the nose cap. In this case, I've cleaned it up and will leave it. After all, it's hand made and not store bought. Air pockets or voids will also appear every once in a while. This is usually caused from the molten metal from cooling down too rapidly and the air which is forced out of the cavity gets trapped. Some times you can do a tiny re-pour. This can be scary and quite dangerous. Safety first!