kuraki
Fimbulvetr Knifeworks
- Joined
- Jun 17, 2016
- Messages
- 4,679
I you can't see a vague outline of the hamon right out of the quench, it probably isn't going to look very good when finished.
Yeah. At least the difference in decarb. Like this:

So, one other thing Tom. When I'm done thermal cycling I clean the blade to 120 past any decarb the cycling created. Then clay and quench. Because of that, I always see a difference like the picture above since the clay is protecting what's under it from oxygen. That's not however necessarily indicative of the resulting hamon. That blade looked like this at 80 grit:
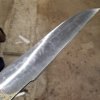
And then 400 grit off the disc:
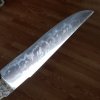