- Joined
- Nov 15, 2005
- Messages
- 1,198
So I recently did some testing on a blade that I "botched" the heat treat on. This was before I build my new, easy to control, forced air burner...
I estimate that I quenched this blade @ around 1,700+ F. The over heating of the blade is apparent with this blistering pattern.
(Yall taught me this in this thread https://www.bladeforums.com/threads/is-this-what-decarb-looks-like.1615017/)

Since I know that this blades HT was botched, I decided to use it as a test knife. I tempered it with two - 2 hour cycles @ 410F. After tempering I ground though "blistered" surface finish. I then attached micarta handle scales with G-Flex epoxy and 2 brass corby fasteners.
I also wanted to see how hard it was to get the scales to part from the handle.
------------------------------------------------------------------------------------
So to my fun theoretical question (that I'll have to empirically test with a non-botched knife)... Do yall think the performance of this knife was on par or worse than if I hadn't botched the HT temperature?
To re-phrase: How do you think a 1084 blade quenched at 1,500 F would have compared to this blistered blade?
Bonus: How much would you expect a knife like this to flex in degrees before breaking if the HT was on point and the hardness was targeted @ around 58-60 HRC?
It was fun to break this guy... I'm just wondering some of these things out loud here.
Cheers!

Actual testing starts around 1:50
Edit:
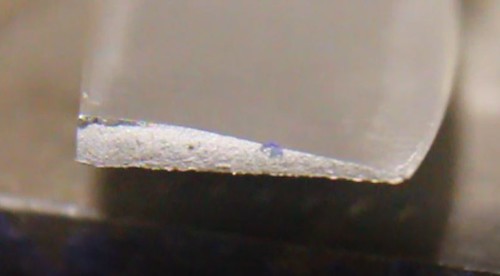
I estimate that I quenched this blade @ around 1,700+ F. The over heating of the blade is apparent with this blistering pattern.
(Yall taught me this in this thread https://www.bladeforums.com/threads/is-this-what-decarb-looks-like.1615017/)

Since I know that this blades HT was botched, I decided to use it as a test knife. I tempered it with two - 2 hour cycles @ 410F. After tempering I ground though "blistered" surface finish. I then attached micarta handle scales with G-Flex epoxy and 2 brass corby fasteners.
I also wanted to see how hard it was to get the scales to part from the handle.
------------------------------------------------------------------------------------
So to my fun theoretical question (that I'll have to empirically test with a non-botched knife)... Do yall think the performance of this knife was on par or worse than if I hadn't botched the HT temperature?
To re-phrase: How do you think a 1084 blade quenched at 1,500 F would have compared to this blistered blade?
Bonus: How much would you expect a knife like this to flex in degrees before breaking if the HT was on point and the hardness was targeted @ around 58-60 HRC?
It was fun to break this guy... I'm just wondering some of these things out loud here.
Cheers!

Actual testing starts around 1:50
Edit:
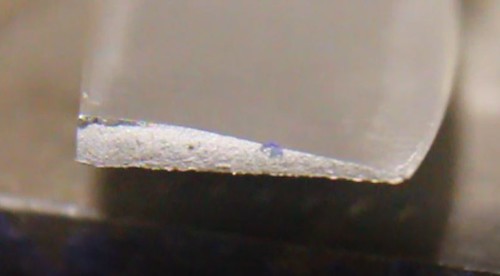
Last edited: