- Joined
- Jul 8, 2014
- Messages
- 558
I just started working on this English Spear and Jackson 3.5 lb axe. I believe its a 50’s or 60’s vintage made from Sheffield steel (according to their catalogue.) The poll filed nicely, and then I started working on the edge. Wow! I sanded 1/2” up on either side of the edge with the orbital sander to avoid filling my files with crap. I have refurbished approximately 60 axes now, and this is without a doubt the hardest steel I have ever encountered. Only one of my files touched it! It’s going to be a labour of love! If anyone has any suggestions regarding what might touch this kryptonite, I am wide open to your ideas.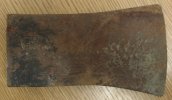
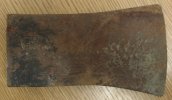