This is the first knife that I'm calling finished.
I ruined a few before this one.
I ground 6 blades before this one, some were decent, some were really bad.
It's 52100 that I forged and heat treated myself so it's probably not a very good blade unless I got lucky.
1. I brought it a couple shades past non-magnetic for 10 mins then air cooled. ( not welding temps by any means, but pretty bright)
2. I brought it just past magnetic for 10 mins then air cooled.
3. I brought to just under magnetic for 10 mins then air cooled.
4. I brought just past magnetic, and quenched in 130 degree canola oil.
It was very hard at this point, a file won't cut it at all.
Then I finish ground the blade and tempered it twice for two hours at 400.
It gets extremely sharp, but I don't know how tough it is.
I'm pretty happy with the design.
I just wanted a good all around hunting/skinning knife.
I ordered some 1084 so I can ht myself and at least know that I have a working knife.
Hopefully the pictures show up.
Let me know what you think.
Thanks.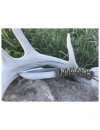
I ruined a few before this one.
I ground 6 blades before this one, some were decent, some were really bad.
It's 52100 that I forged and heat treated myself so it's probably not a very good blade unless I got lucky.
1. I brought it a couple shades past non-magnetic for 10 mins then air cooled. ( not welding temps by any means, but pretty bright)
2. I brought it just past magnetic for 10 mins then air cooled.
3. I brought to just under magnetic for 10 mins then air cooled.
4. I brought just past magnetic, and quenched in 130 degree canola oil.
It was very hard at this point, a file won't cut it at all.
Then I finish ground the blade and tempered it twice for two hours at 400.
It gets extremely sharp, but I don't know how tough it is.
I'm pretty happy with the design.
I just wanted a good all around hunting/skinning knife.
I ordered some 1084 so I can ht myself and at least know that I have a working knife.
Hopefully the pictures show up.
Let me know what you think.
Thanks.
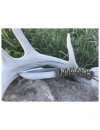