weo
Basic Member
- Joined
- Sep 21, 2014
- Messages
- 3,032
Hello all. It's time for me to put my forge back together and I think I'm going to make some upgrades. Here's a sketch of my original set-up:
And here's a schematic of what my plan is: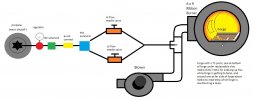
My initial upgrade idea was to install a NC valve right at the tank regulator connected to the blower wiring so that fuel is shut off when the blower isn't running, but that quickly morphed into adding the PID controller system. I don't intend on using this as a HT forge, I just want to try to improve my efficiency with fuel use.
This will probably be a WIP and I'm sure I'll have questions along the way. In fact, here's one: does it matter if I wire the NC solenoid in series or parallel with the blower?
Thanks
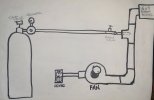
And here's a schematic of what my plan is:
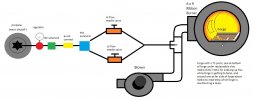
My initial upgrade idea was to install a NC valve right at the tank regulator connected to the blower wiring so that fuel is shut off when the blower isn't running, but that quickly morphed into adding the PID controller system. I don't intend on using this as a HT forge, I just want to try to improve my efficiency with fuel use.
This will probably be a WIP and I'm sure I'll have questions along the way. In fact, here's one: does it matter if I wire the NC solenoid in series or parallel with the blower?
Thanks