CPE_Knives
Knifemaker / Craftsman / Service Provider
- Joined
- Oct 29, 2012
- Messages
- 1,524
I've always wanted to build traditional Japanese knives and after the last few projects with all the copper work and fittings I felt like I had the skills to take one of these on.
I decided to try and recreate a tanto made by Shintogo Kunimitsu around the year 1300. I was able to get a kata and drawing of the original that is in the Tokyo National Museum.
I started the pictures just before heat treat and as I write this the only steps left are the ito wrap and a final polish.
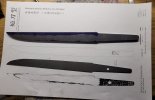
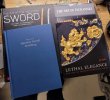
I decided to try and recreate a tanto made by Shintogo Kunimitsu around the year 1300. I was able to get a kata and drawing of the original that is in the Tokyo National Museum.
I started the pictures just before heat treat and as I write this the only steps left are the ito wrap and a final polish.
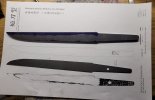
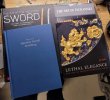
Last edited: