- Joined
- Dec 9, 2015
- Messages
- 392
The time has finally come for me to build myself a 2x72. After a lot of window shopping I've decided that I really like the dcknives style grinder and want my build to be based on this, but with step pulleys. So far all I have is a motor and a rough plan. I also have plenty of tools and enough experience to handle the actual construction. I do have some design questions though.
Some background that I hope will be helpful:
I'm a hobby maker, I aspire to be good enough to make sell-able knives but I have no intention of going pro.
I'm working out of a shed with a single 110v/15a outlet, which is why I went with a 1hp (13a) motor. I'm renting so this is not going to change for at least a few years.
My primary interests are traditional pocket knives and kitchen knives, but I like making any sort of knife or tool that I might need. I'm the kind of person who sees something cool and my first thought is "How can I make that?" so I'd like to keep my grinder as versatile as possible.
On to the questions!
1) The dcknives grinder has a vertical, telescoping tracking arm. The KMG style lever arm seems like it would be more ergonomic, but will there be enough real-world difference for it to matter? Any differences in grinder performance or trickyness of construction?
2) When I have the shaft behind/below the grinder with a step pulley on one end and drive wheel on the other, will I need two pillow block bearings or will just one do it? Even if just one will do it, will two be better?
3) I made a spreadsheet of potential wheel/pulley combos, what do you guys think of these speeds for an all around knife making (steel, brass, wood, G10, bone, etc) grinder? My current 1x30 runs at (claimed) 3260 SFPM. With Blaze belts it cuts steel well enough, but it burns the heck out of wood and gets brass very hot very fast.
The SFPM column is highlighted. I'm worried that trying to go too fast on the highest speed will bog the motor. I can bog my little HF sander just by looking at it the wrong way and for all this time and money spent I don't want to have to worry about that under normal use.
Thanks for reading!
Some background that I hope will be helpful:
I'm a hobby maker, I aspire to be good enough to make sell-able knives but I have no intention of going pro.
I'm working out of a shed with a single 110v/15a outlet, which is why I went with a 1hp (13a) motor. I'm renting so this is not going to change for at least a few years.
My primary interests are traditional pocket knives and kitchen knives, but I like making any sort of knife or tool that I might need. I'm the kind of person who sees something cool and my first thought is "How can I make that?" so I'd like to keep my grinder as versatile as possible.
On to the questions!
1) The dcknives grinder has a vertical, telescoping tracking arm. The KMG style lever arm seems like it would be more ergonomic, but will there be enough real-world difference for it to matter? Any differences in grinder performance or trickyness of construction?
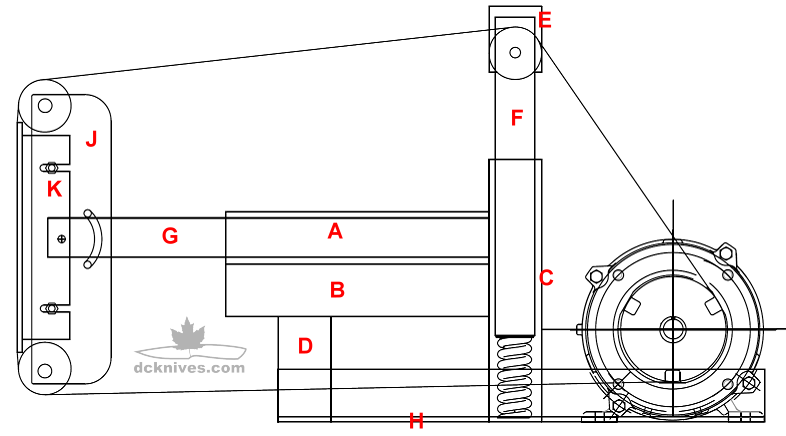
2) When I have the shaft behind/below the grinder with a step pulley on one end and drive wheel on the other, will I need two pillow block bearings or will just one do it? Even if just one will do it, will two be better?
3) I made a spreadsheet of potential wheel/pulley combos, what do you guys think of these speeds for an all around knife making (steel, brass, wood, G10, bone, etc) grinder? My current 1x30 runs at (claimed) 3260 SFPM. With Blaze belts it cuts steel well enough, but it burns the heck out of wood and gets brass very hot very fast.
The SFPM column is highlighted. I'm worried that trying to go too fast on the highest speed will bog the motor. I can bog my little HF sander just by looking at it the wrong way and for all this time and money spent I don't want to have to worry about that under normal use.

Thanks for reading!