- Joined
- Nov 15, 2005
- Messages
- 1,198
Hey guys, I'm messing around with a DIY HT oven in my shop and have been having some issues. For some reason my oven is maxing out around 1315F.
I was hoping someone may have some ideas on what my problem is. I'm hoping it's just my lack of experience with this Auber 2352P controller.
Build:
Chamber Size = 5'' tall x 6.5'' wide x 18'' long
Chamber Volume = 0.3385 ft3
Chamber Construction = soft fire brick plus 1'' ceramic blanket
Elements = 16 AWG Kanthal A1 wound to a 0.4766'' diameter
Element Resistance = 17.8 ohms
Oven Electronic Specs = 240V, 3236 watts, 13.5 amps
Watt/ft3 = 9559
Elements are run in 2 U-shape paths along the two inner walls (none-along the back). These two coils are wired in series with a 10 AWG jumper outside of the oven in the back. Ohms are confirmed @ 17.8 with meter. The total path length of both sides combined is 71 inches (total stretched coil length)
Wiring diagram:
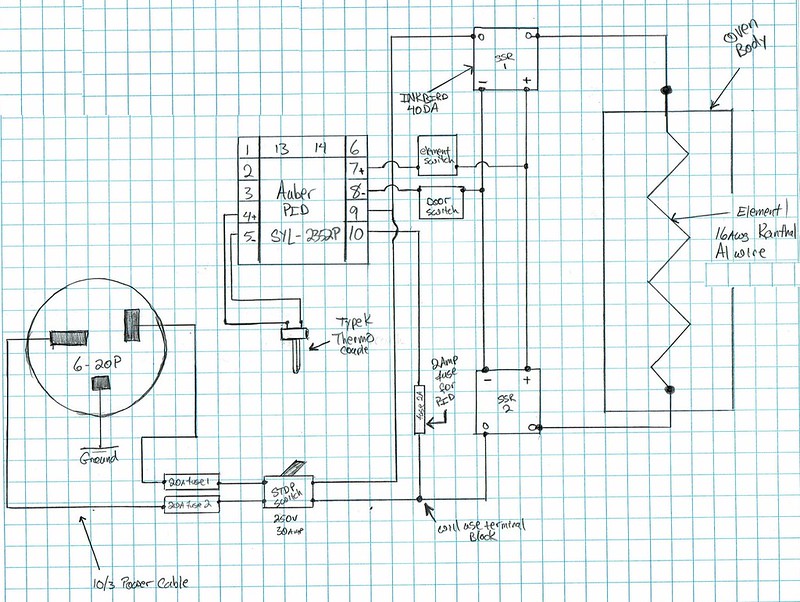
~12' of 10/3 power cable running from a dedicated 20 amp 6-20P. All oven internal box wiring is high temp 12 AWG and the runs to the elements are 10 AWG high temp.
I cut this 14.5'' thermocouple down to ~6'' in length... not sure if that could be an issue? I ran new type K TC wire from KilnParts.Com. It appears to be reading the ambient temperature accurately before start up.
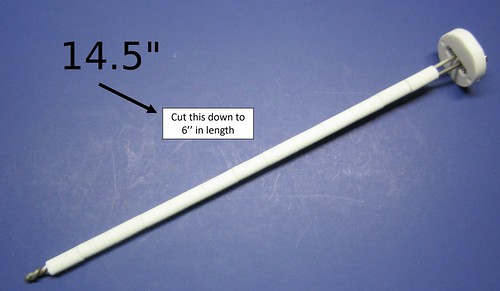
Auber 2352 P:
I've tried a bunch of different PID configurations in the controller including a straight proportional control with I and D zeroed out (P60,I0,D0). I figured this would ramp quickly for a test. It still maxed at 1300. The graph is for the default settings for the PID values:

If also tried to AT from both the 1300 range and zero without better results.
The settings on the alarms have all been set to their maxes (not sure if that matters anyway... if it's alarming or not that is?... since I don't have an alarm wired into the PID).
"COOL" is set to 10 which should mean it's reading in F
Program:
C01 = 1975
T01 = 1
C02 = 1975
T01 = 150
C03 = -1
T03 = -1
repeated to 30
Thanks for any help guys! I basically have an expensive door jam at this point...
J. Keeton
I was hoping someone may have some ideas on what my problem is. I'm hoping it's just my lack of experience with this Auber 2352P controller.
Build:
Chamber Size = 5'' tall x 6.5'' wide x 18'' long
Chamber Volume = 0.3385 ft3
Chamber Construction = soft fire brick plus 1'' ceramic blanket
Elements = 16 AWG Kanthal A1 wound to a 0.4766'' diameter
Element Resistance = 17.8 ohms
Oven Electronic Specs = 240V, 3236 watts, 13.5 amps
Watt/ft3 = 9559
Elements are run in 2 U-shape paths along the two inner walls (none-along the back). These two coils are wired in series with a 10 AWG jumper outside of the oven in the back. Ohms are confirmed @ 17.8 with meter. The total path length of both sides combined is 71 inches (total stretched coil length)
Wiring diagram:
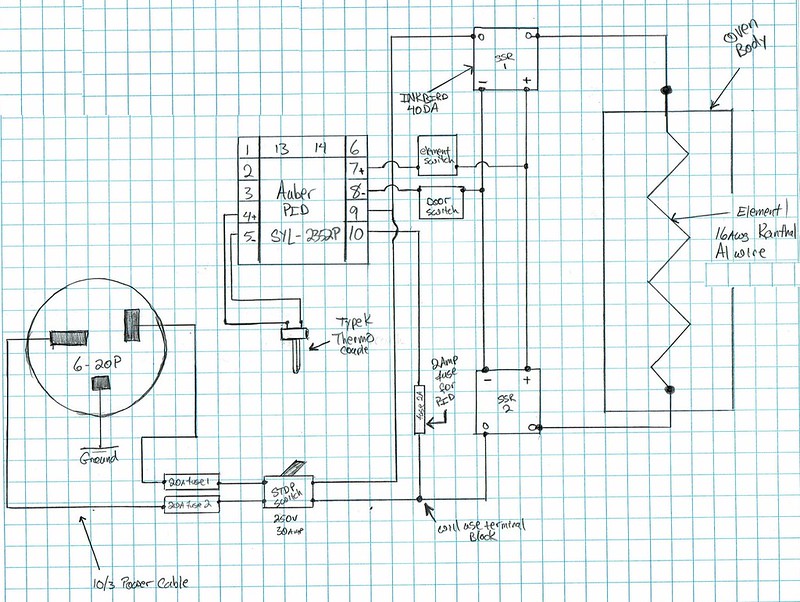
~12' of 10/3 power cable running from a dedicated 20 amp 6-20P. All oven internal box wiring is high temp 12 AWG and the runs to the elements are 10 AWG high temp.
I cut this 14.5'' thermocouple down to ~6'' in length... not sure if that could be an issue? I ran new type K TC wire from KilnParts.Com. It appears to be reading the ambient temperature accurately before start up.
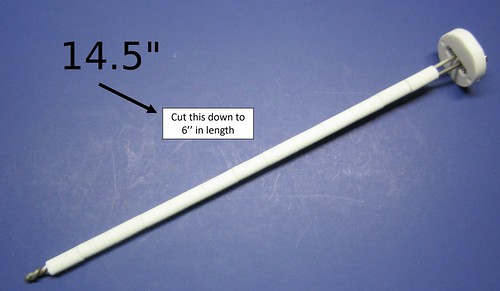
Auber 2352 P:
I've tried a bunch of different PID configurations in the controller including a straight proportional control with I and D zeroed out (P60,I0,D0). I figured this would ramp quickly for a test. It still maxed at 1300. The graph is for the default settings for the PID values:

If also tried to AT from both the 1300 range and zero without better results.
The settings on the alarms have all been set to their maxes (not sure if that matters anyway... if it's alarming or not that is?... since I don't have an alarm wired into the PID).
"COOL" is set to 10 which should mean it's reading in F
Program:
C01 = 1975
T01 = 1
C02 = 1975
T01 = 150
C03 = -1
T03 = -1
repeated to 30
Thanks for any help guys! I basically have an expensive door jam at this point...
J. Keeton