- Joined
- Oct 10, 2018
- Messages
- 455
Exciting times. This build is very nearly finished! I ended up re-drilling on the chuck to make it straighter before I dress it on the wheel. This will help to not grind a lopsided amount off of one end. It will also make dressing go faster, I believe. I also added a wingnut to one side so that I can do tapered tangs (I am also thinking about how I could taper scales to a high degree of symmetry to make handle shaping easier). I came up with using some PVC pipe on top of the handle bolt, just to make an easier grip. I'm pretty happy with how that turned out.
After this build, I've decided that I should be done drilling aluminum for a while
Things left to do:
1. Bolt the 2x72 frame to the table
2. Surface grind the chuck (need to take off a bit of material to get closer to the magnets anyway)
3. Raise the shield a bit so that the belly of a blade couldn't ramp off the edge and fly across the shop if the wheel launches a blade
4. Mount a cheap dial indicator
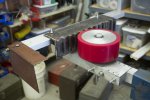
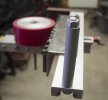
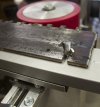
After this build, I've decided that I should be done drilling aluminum for a while

Things left to do:
1. Bolt the 2x72 frame to the table
2. Surface grind the chuck (need to take off a bit of material to get closer to the magnets anyway)
3. Raise the shield a bit so that the belly of a blade couldn't ramp off the edge and fly across the shop if the wheel launches a blade
4. Mount a cheap dial indicator
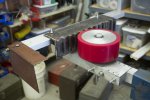
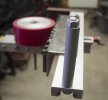
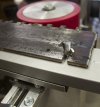