The wavy surface might be partly due to slight eccentricity in your contact wheel. I trued up my contact wheel using a flat piece of steel with some sandpaper attached with spray glue. I posted a thread about it here:
www.bladeforums.com
Truing up an SGA contact wheel
I just built a surface grinding attachment and noticed some slight waviness in the surface finish of the test pieces I ground. The amplitude of the waves is very small and barely makes the needle on my test indicator move, but it is pretty visible by eye, even though it is very difficult to...
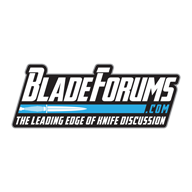