
This is a photo (above) from Josh.
Mine (below) isn't as good:
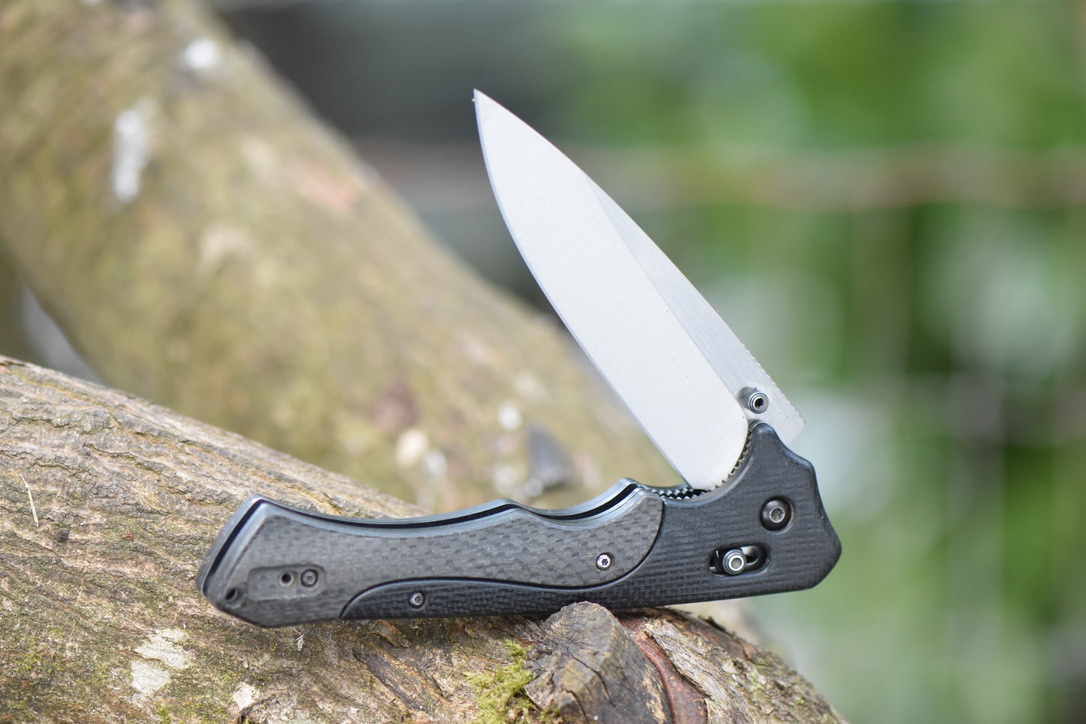
I just got my oldest Rukus 610 (first production run) back from Josh at Razor Edge Knives. Josh had to do a lot of legwork to make this project work. (Many thanks)
The idea was to take a large, strong and durable knife platform — the Benchmade Rukus 610 — and give it a super tough, upgraded steel with a world class heat treat. I chose A8-mod steel, which is about as tough a knife steel as you’ll find. It’s the steel of choice for things like wood chipper blades.
A8-mod is a medium carbon steel with added chromium, molybdenum and vanadium. Of course, steel is only as good as the heat treat. Fredrik Haakonsen, a renowned Norwegian knife maker with a PhD in metallurgy, agreed to provide the steel with longitudinal grain pattern (for even more strength) and his famous and elaborate heat treat.
Haakonsen likes to use A8-mod because it’s far less likely to break or chip than high-alloy steels under hard use, even at Rc 60-61, which is this blade’s hardness. With that hardness (hardness is a good proxy for strength, or resistance to rolling or bending) and the incredible toughness of A8-mod, the edge retention on this steel exceeds even high-wear powder steels under hard use. If you get lost in the wilderness, this is a good knife to have in your pocket.
The upgraded steel and edge retention allowed Josh to grind the edge thinner than the stock blade — down to about 0.017 inches at the shoulders with a 30 degree inclusive bevel. It easily out slices the stock blade and almost any other factory blade, while retaining its incredible toughness.
If you read this far, the reward is a puppy photo -- Haley the three-month-old GSD.
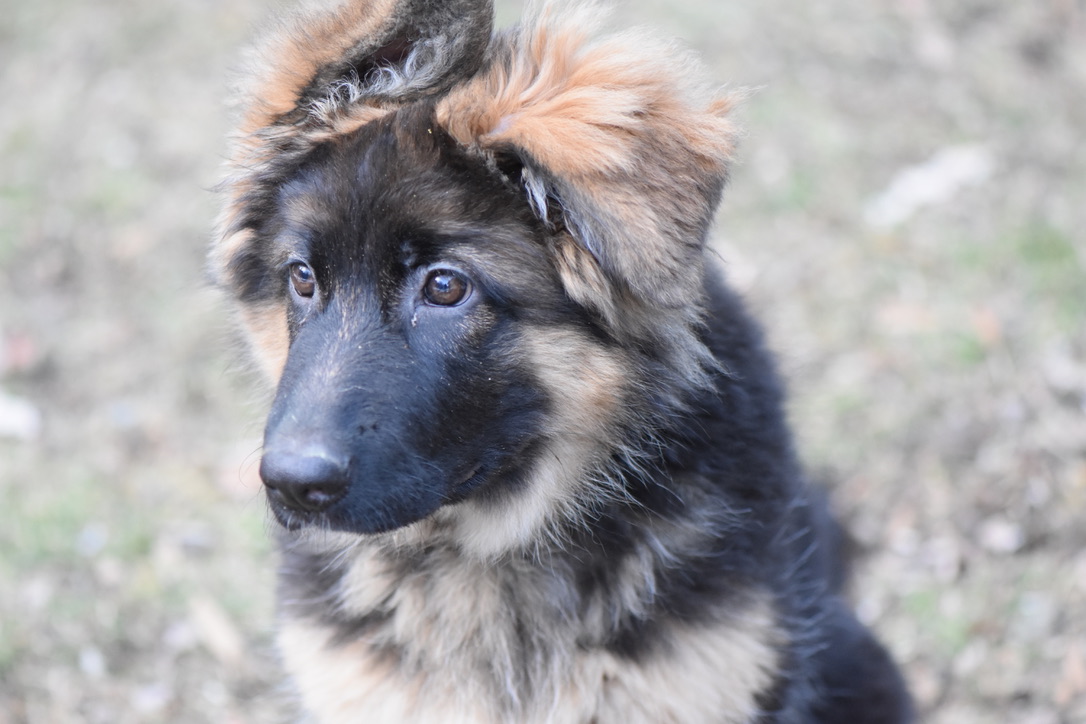
Last edited: