3: Do yall clean up the edges during stacks?
Sometimes (depending on my mood, mainly), but there is a significant benefit from grinding all edges flush, especially when using a press for forge-welding.
Anytime you do forge-welding when the pieces aren't exactly the same, unless you are
extremely careful and skilled, you will get cold shuts/scale lines along the seams. And never think you can forge out a crack or seam, you will only be able to forge it deeper into the billet. So grinding all pieces flush will help minimize these seams. Any this is more important (IMO) when going for mosaic-type patterns opposed to the more random patterns.
Lately, I've been grinding my initial 15-25 layer stack of 1080/15N20 clean on all sides, but not subsequent cut and stacks, because in the initial stack, I could end up with 24 cold shuts or seams, but the rest of the stacks will only have 2-4.
what target size stock should I start with to forge my blade?
Totally dependent on your abilities and tools. The larger the starting stock, the more material you have to move around. The smaller the stock is, the more risk you have of not having enough....
Personally, I worry more about what the final forging size should be taking into account thickness losses from scale, forging marks, etc. Lately, it seems like my pieces lose about .015" per side when going from the anvil to the surface grinder to give me true flats. That usually takes care of all decarb for the pattern as well.
I'd love to hear some "steel conservation" tips
-Keep a reducing atmosphere in the forge during the entire forging process to minimize scale formation
-Be
extremely diligent with brushing scale off the billet and your press and anvil
-Make stick tang knives instead of full tang
It doesn’t seem right to cut and stack after you made your rain drops.
According to Jim Hrisoulas in his book "The Pattern Welded Blade", his technique is to drill holes, flatten, cut, stack, re-weld and then drill holes a 2nd time before forging the profile for a raindrop pattern. I haven't used his method, only drilling the holes at the end. I bet it would look good if you doubled your billet, and maybe even drilled a few more shallow holes? (if you have enough material, that is).
Another thing I've done on my last few raindrops was to use 2-3 different drill bit sizes for the holes and I like that.
Especially since I can still see circles.... Gotta keep grinding this piece I think
Is this what you're talking about? The edges if the drill holes?
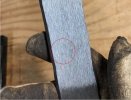
If so, I'm not sure I'd worry about that, especially if it looks like that will go away during your final grinding. One way to minimize this is to chamfer the drill holes to relieve the hard corners just like you do with a ladder pattern.