So here's the photo of both sides done:
And the same on edge(i worked those transitions to be kind of abrupt;they form the scarfs of the poll-weld and need to come together positively):
Now it's time to think of blade steel.Way too cold to use PH to work up some spring,so i end up using this old circular saw-blade i was given some years ago by Mark Knapp.I think he said it May've been L6,since,i started thinking it's more likely 15N20,but in any case i've bladed tools with it before,and it lends itself well to simpler HT(i take a chunk out of the "hub" of it where it's slightly thicker,just a touch under 1/4"):
Another thing i'm attempting to pay more attention to is welding itself.Bad enough that i'm using junk,i must try to be more careful and systematic.I'll not weld this as an ugly 3-and more part sandwich,i'll weld the steel to one side of pre-form first,then close and weld the second half over it.
It is a more responsible method.Less air intervening between composite parts,heat distributed more evenly.Axes are the worst things to weld-wide and flat and very difficult to heat throughout and evenly.
No welding or wire,i'll just hold the steel with the preform like with a shovel;that's how chisels and many other tools were steeled,higher-melting point low-C iron in the fire,more delicate edge steel on top,protected by iron from blast and more likely to be up in the zone of reducing Atm.
Here it is right after welding.It has the appearance of being very thin.It's an illusion,due to it's developing convexity.I welded it edge steel down to the anvil,and in the process the iron outside
got pretty convex(?)...:
\
And this is it,steeled,and tentative lines again re-drawn,with drift offered up.
I misplaced the bit in welding just a tad,IF this head survives,it'll be slightly longer in the eye fore-and-aft.That last photo shows that:
(i hear people complaining about this often...and am appropriately grieved...but i was lucky as it was, to slap it down where it landed,it slip-sliding all over on molten flux
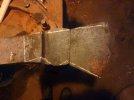
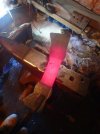
And the same on edge(i worked those transitions to be kind of abrupt;they form the scarfs of the poll-weld and need to come together positively):
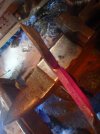
Now it's time to think of blade steel.Way too cold to use PH to work up some spring,so i end up using this old circular saw-blade i was given some years ago by Mark Knapp.I think he said it May've been L6,since,i started thinking it's more likely 15N20,but in any case i've bladed tools with it before,and it lends itself well to simpler HT(i take a chunk out of the "hub" of it where it's slightly thicker,just a touch under 1/4"):
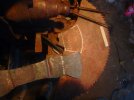
Another thing i'm attempting to pay more attention to is welding itself.Bad enough that i'm using junk,i must try to be more careful and systematic.I'll not weld this as an ugly 3-and more part sandwich,i'll weld the steel to one side of pre-form first,then close and weld the second half over it.
It is a more responsible method.Less air intervening between composite parts,heat distributed more evenly.Axes are the worst things to weld-wide and flat and very difficult to heat throughout and evenly.
No welding or wire,i'll just hold the steel with the preform like with a shovel;that's how chisels and many other tools were steeled,higher-melting point low-C iron in the fire,more delicate edge steel on top,protected by iron from blast and more likely to be up in the zone of reducing Atm.
Here it is right after welding.It has the appearance of being very thin.It's an illusion,due to it's developing convexity.I welded it edge steel down to the anvil,and in the process the iron outside
got pretty convex(?)...:
\
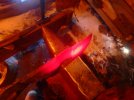
And this is it,steeled,and tentative lines again re-drawn,with drift offered up.
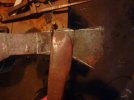
I misplaced the bit in welding just a tad,IF this head survives,it'll be slightly longer in the eye fore-and-aft.That last photo shows that:
(i hear people complaining about this often...and am appropriately grieved...but i was lucky as it was, to slap it down where it landed,it slip-sliding all over on molten flux

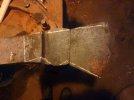