So I got my steel back from my buddy. The cutting wasn't perfect, as detailed below. And he just handed me a big box of steel parts. The steel and the water jetting was free, so I don't mind having to do some tweaking.
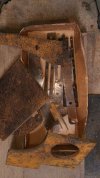
First, I wanted to finish drill and tap the left side plate. The holes get tapped for the bolts that hold the pieces that form the two tool arm pockets. The alignment is critical and I wanted to know right away if there was an issue. To keep the small cut outs from the water jet cut holes from falling down into the water jet cutting tank, they are retained with a small tab. The pieces knock out really easily with a punch, but the tab remnant needs to be removed by drilling with a 1/4"-20 tap drill. This may not be an issue with other water jet setups, but hey, it's free.
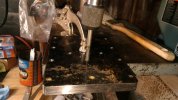
Next is the spacers that form the pocket. There are 3 long ones and 6 smaller. The long ones are the separators for the top and bottom pocket, the smaller ones form the top of the top one, and the bottom of the bottom one.
Finish drilling the 1/4" through holes on the spacers.
The water jet is supposed to make a nice clean edge. Something was off on the machine making it think it was cutting thinner material than the 1/2" plate used. This caused some edges to be uneven. Did I mention it was free?
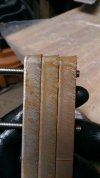
I bolted the spacers together with the side plate to even them out with the profile of the tapped side plate. This goes to the outside and will not effect the pocket dimensions, I just want it to look nice. I will true up the interior faces if I have an issue with the tool arm clearance. Good thing I already have a 2x72 to make quick work of this.
Next is a trial fit up of the pockets- looking good.
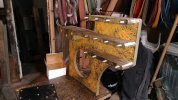
Because we are super classy here, I had my logo cut into the main upright.
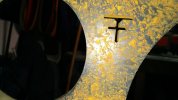
My fancy pants knobs to lock the tool arms fit well.
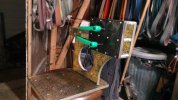