So - with a little time for people reading this to digest what I have tried to put out there, I thought I would close this thread out, at least for now, with a few thoughts and conclusions of my own.
First, in order to do a reasonable job of home-stabilization, there are a number of things to be aware of and to monitor:
- make sure the wood is dry (and know just how dry it is - it is better to dry to a higher degree in a kiln or drying box)
- be aware of the type of wood you are stabilizing - and more specifically be aware of the pore size distribution in that wood (if the distribution is slanted more towards the smaller pores, then you are not going to get the degree of pore-filling you might be after
- resin viscosity is not necessarily going to affect your degree of penetration of the wood - BUT with the more viscous resins you need to allow more "soak" time at pressure to allow the resin time to flow into the deepest pore spaces.
- When you pull a vacuum - make sure your equipment allows you to pull to a low enough pressure - AND allow enough time under vacuum to both evacuate air, and to allow more moisture to de-adsorb from the pore surfaces
- Allow sufficient "soak" time after relieving the pressure to allow the resin to flow into the pores as completely as it can
- know the quality of your resin - avoid "pre-activated" resin, and strive to use domestically-produced resin
From the above, it should be clear that there are a LOT of ways in which stabilization can be messed up. Given that - you might want to consider whether you want to trust stabilized wood done by "just anybody" out there (from Etsey for example), and also whether you want to trust
yourself to get the steps right. some will trust themselves, at which point you can probably do a reasonable job (especially with woods that tend towards the larger pore distributions - spalted woods being an extreme case of wood with a lot of very large pores).
Always be aware, though, that you will simply not be able to get the same degree of resin penetration that the professional houses can (with their 4000 psi final "push" of resin through the smaller pore throats). If your objective is a straightforward "heavier is better" - then I think there is no argument that having the stabilization done professionally is the better approach. Also keep in mind, as several have pointed out, that it is not necessarily less expensive to do the stabilization yourself.
On the other hand, however, there are two factors I can think of that might drive you towards stabilizing yourself. First is turnaround time. Doing the stabilization yourself will take, maybe, 2-4 days. Turnaround time to have wood sent out and done at the professional shops will likely take weeks to months. You will have to decide which is more important. The second is the point that started me thinking about this in the first place: How much resin penetration is "good enough"? If your objective is not sheer weight/heft of the wood, how much resin penetration is "good enough"? As several have pointed out, woodworkers stabilize their own wood, then put it onto things like, a lathe, and spin at high rates while pushing sharp objects into the material. If your objective is sheer
mechanical stabilization, then, especially for those woods that
really need it precisely because they are loosely held together, and thus by definition have mostly large pores (like spalted woods, or some burls) then you can probably do quite a suitable stabilization yourself - but again, the result will likely be lighter than if done professionally.
For example, I obtained a number of samples of spalted wood from WEO that he sent out for stabilization (he did not do the actual stabilization). some are not-yet-dry, some were professionally stabilized, and a couple were non-professionally stabilized (stabilization sources remain anonymous). One of them, dyed green, was obviously, by feel, less dense than the wood coming back from professional stabilization. Here it is:
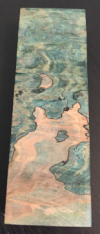
The outside, by probing with both fingernail and metal punch, is pretty hard everywhere. When cut in half for scales:

It is clear (again by probing with fingernail and punch) that in the highly sparled regions, the resin has for the most part penetrated and the material is hard, but in the not-so-highly sparled regions (the lighter colored areas) there is little or no resin (it is softer). But, these un-penetrated regions are well held together, and there is no sense these scales will just fall apart. It is good enough for put on as handle for a modified paring knife I am working on for myself and family - but no way I would put it on a knife I am planning to sell. (another piece of non-professionally stabilized wood is basically as dense as the professionally stabilized wood - and might very well be suitable for sale, or perhaps on a knife given as gift to friend or family. It depends.
What I have tried to do here in this thread by getting into the details is to de-mystify the stabilization process, hopefully to get past the differing opinions on professionally versus home stabilized wood. I believe those differing opinions have arisen from both different expectations and "needs" for the stabilized wood, combined with some truly bad experiences of "home stabilized" wood that was either done really badly (because of bad process and control of the process), or done on a wood that is just not suitable for home stabilization - but that does not mean that with the proper process, and appropriate choice of wood, that home stabilization is not an appropriate option (I believe it is).
Hopefully people have found this little exercise worthwhile....
For the record, I have some un-stabilized spalted wood that is now dry and ready for stabilization. I will be sending that out to a professional house for dying and stabilization. I would be interested in stabilizing that spalted wood myself - but right now dont want to invest the $$$'s in the equipment, and for its purpose I can afford the wait for the turnaround time......