Cushing H.
Gold Member
- Joined
- Jun 3, 2019
- Messages
- 2,714
Next posting - Surface Tension.
What gets in the way of filling the porespace with resin? – Surface Tension
Ok … this is the big one to understand – and will take pictures and one equation.
Any time you have an interface between two different fluids, there is a tension in the interface. The reason for this comes from both thermodynamics (and free-energy based “incompatibilities” between the fluids) and also from force balances between the molecules of the fluids. For now – maybe just think of it as a situation where the physics involved do not like the fluids to be intermixed – and so the forces involved try to minimize the contact area between the two. So the situation looks something like this:
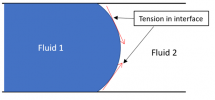
If you think about this drawing, the tension in the interface (“surface tension”) will act to pull that interface back into a “flatter” surface, thus reducing the area of contact between the two fluids. By the way – any gas is a fluid, as is any liquid – so the term “fluid” here is pretty general. The contact could be between two liquids (ex. Oil and water), or a liquid and a gas (water and air, oil and air, acrylic resin and air, etc). A vacuum is not quite a “fluid” – but the same rules giving rise to surface tension arise when a liquid (like oil or acrylic resin) has an interface between it and a vacuum – that interface will have a surface tension present.
Think of the interface kind of like the surface of a balloon: if you inflate the balloon, the pressure inside the balloon goes up, and the surface of the balloon develops a tension in it (you feel that tension as the surface of the balloon becoming “harder”). The interface between two fluids is similar – with the only difference being that the tension of the interface (in units of force per unit length) does not go up as the pressure inside the interface goes up – the surface tension is constant defined only by the materials. I know this might sound a little counter-intuitive, but it is the way it is….
Now – any time that interface between fluids is curved, just like a balloon, there is a pressure difference from one side of the interface to the other (higher pressure being on the concave side of the interface). This pressure difference is described by the “Young-Laplace” equation (different disciplines might have different names for this relationship – but the equation is the same). That equation is:
(pressure difference) = 2 * (surface tension) / Radius
Here, “pressure difference” is the pressure difference across the interface, “surface tension” is the surface tension of the interface (remember, this is defined strictly by the two materials involved), and “radius” is the radius of curvature of the interface.
This is pretty visually intuitive: in the following picture:
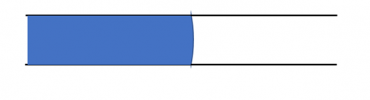
The interface has a large radius of curvature, and so the pressure difference across the interface is low. On the other hand, in the picture below:
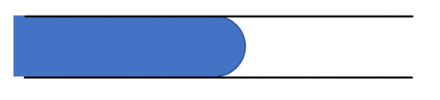
The radius of curvature of the interface is small – and so the pressure on the left side is much higher.
The other thing to know about this is that the Young-Laplace equation describes an equilibrium (“steady-state”) situation. If the radius of curvature and the pressure drop present do not satisfy the Young-Laplace equation, the situation is physically unstable, and either the radius of curvature will change, or the location of the interface will physically move to find a location / geometry where the equation can be satisfied.
Another thing to know is this: there is something very peculiar about where the interface meets the walls around it, that location indicated by the red circle below:
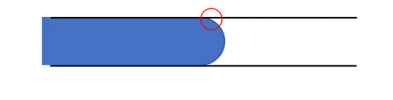
Blown up to a larger scale, that location is a single point that represents the common meeting of three different materials, “fluid 1”, “fluid 2”, and the solid surface bounding them:
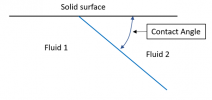
Now … the peculiar thing about this point of contact between three materials is that the thermodynamics (really the free energies of the materials) strictly defines the contact angle. That angle is fixed – and it does not depend at all on the pressure from one side of the interface to the other.
The result of all this is that – for an interface (like the interface of acrylic resin and vacuum on the pores) to be stable – both the curvature relationship of the Young-Laplace equation and the contact angle must be simultaneously satisfied. If they are both satisfied, then the interface will stay right where it is. The only way to change that – like to move the interface deeper into the pore system, is to create a situation where the Young-Laplace equation can not be satisfied.
Re-enter into the picture the “model pore system” I started with (I warned you we would be coming back to this……):
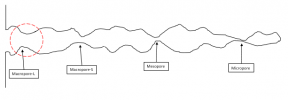
Now, there is something truly unique about those “pinch points” I called pore throats. Lets take a really close up look at the one above indicated by the red dashed circle:
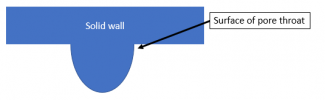
Because of the extreme curvature present at that very small point, it is geometrically possible to continuously satisfy the interface contact angle, even though the radius of curvature of the overall interface changes drastically. Three cases below illustrate this (hopefully).
Low pressure across interface:
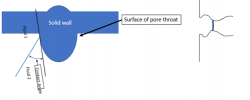
Higher pressure across interface:
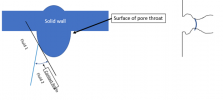
High pressure across the interface:
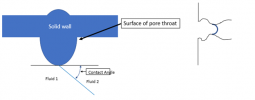
As the pressure across the interface goes up, the radius of curvature of the interface goes down (satisfying the Young-Laplace equation), contact angle continues to be satisfied because the small curvature of the wall at the pore throat allows that with very, very small movement of the actual contact point. The interface essentially is “stuck” at that pore throat, even though pressure from the outside is going up.
The interface is said to be “pinned” at the pore throat.
The upshot of this, for us, is that as you increase the pressure on the resin outside of your wood being impregnated, the amount of resin penetration is NOT continuous, or proportional to pressure, as you increase pressure. Rather (this is somewhat simplified), you can increase the pressure, and continue to increase the pressure, and those interfaces remain “pinned” at the pore throats, and you will NOT get any more resin into the wood.
(NOTE: I'm running into a limit on uploads - will need to split this posting and continue with a part 2....)
What gets in the way of filling the porespace with resin? – Surface Tension
Ok … this is the big one to understand – and will take pictures and one equation.
Any time you have an interface between two different fluids, there is a tension in the interface. The reason for this comes from both thermodynamics (and free-energy based “incompatibilities” between the fluids) and also from force balances between the molecules of the fluids. For now – maybe just think of it as a situation where the physics involved do not like the fluids to be intermixed – and so the forces involved try to minimize the contact area between the two. So the situation looks something like this:
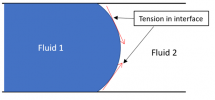
If you think about this drawing, the tension in the interface (“surface tension”) will act to pull that interface back into a “flatter” surface, thus reducing the area of contact between the two fluids. By the way – any gas is a fluid, as is any liquid – so the term “fluid” here is pretty general. The contact could be between two liquids (ex. Oil and water), or a liquid and a gas (water and air, oil and air, acrylic resin and air, etc). A vacuum is not quite a “fluid” – but the same rules giving rise to surface tension arise when a liquid (like oil or acrylic resin) has an interface between it and a vacuum – that interface will have a surface tension present.
Think of the interface kind of like the surface of a balloon: if you inflate the balloon, the pressure inside the balloon goes up, and the surface of the balloon develops a tension in it (you feel that tension as the surface of the balloon becoming “harder”). The interface between two fluids is similar – with the only difference being that the tension of the interface (in units of force per unit length) does not go up as the pressure inside the interface goes up – the surface tension is constant defined only by the materials. I know this might sound a little counter-intuitive, but it is the way it is….
Now – any time that interface between fluids is curved, just like a balloon, there is a pressure difference from one side of the interface to the other (higher pressure being on the concave side of the interface). This pressure difference is described by the “Young-Laplace” equation (different disciplines might have different names for this relationship – but the equation is the same). That equation is:
(pressure difference) = 2 * (surface tension) / Radius
Here, “pressure difference” is the pressure difference across the interface, “surface tension” is the surface tension of the interface (remember, this is defined strictly by the two materials involved), and “radius” is the radius of curvature of the interface.
This is pretty visually intuitive: in the following picture:
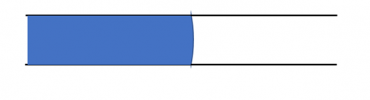
The interface has a large radius of curvature, and so the pressure difference across the interface is low. On the other hand, in the picture below:
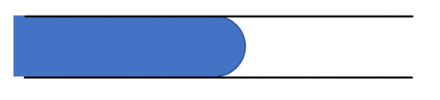
The radius of curvature of the interface is small – and so the pressure on the left side is much higher.
The other thing to know about this is that the Young-Laplace equation describes an equilibrium (“steady-state”) situation. If the radius of curvature and the pressure drop present do not satisfy the Young-Laplace equation, the situation is physically unstable, and either the radius of curvature will change, or the location of the interface will physically move to find a location / geometry where the equation can be satisfied.
Another thing to know is this: there is something very peculiar about where the interface meets the walls around it, that location indicated by the red circle below:
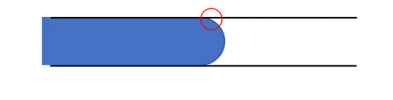
Blown up to a larger scale, that location is a single point that represents the common meeting of three different materials, “fluid 1”, “fluid 2”, and the solid surface bounding them:
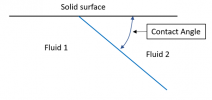
Now … the peculiar thing about this point of contact between three materials is that the thermodynamics (really the free energies of the materials) strictly defines the contact angle. That angle is fixed – and it does not depend at all on the pressure from one side of the interface to the other.
The result of all this is that – for an interface (like the interface of acrylic resin and vacuum on the pores) to be stable – both the curvature relationship of the Young-Laplace equation and the contact angle must be simultaneously satisfied. If they are both satisfied, then the interface will stay right where it is. The only way to change that – like to move the interface deeper into the pore system, is to create a situation where the Young-Laplace equation can not be satisfied.
Re-enter into the picture the “model pore system” I started with (I warned you we would be coming back to this……):
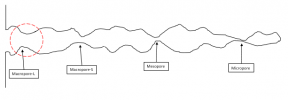
Now, there is something truly unique about those “pinch points” I called pore throats. Lets take a really close up look at the one above indicated by the red dashed circle:
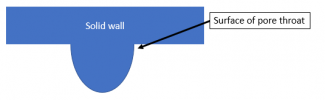
Because of the extreme curvature present at that very small point, it is geometrically possible to continuously satisfy the interface contact angle, even though the radius of curvature of the overall interface changes drastically. Three cases below illustrate this (hopefully).
Low pressure across interface:
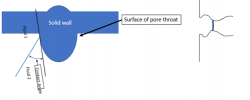
Higher pressure across interface:
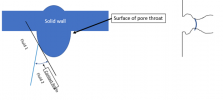
High pressure across the interface:
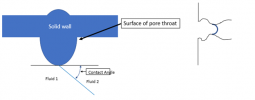
As the pressure across the interface goes up, the radius of curvature of the interface goes down (satisfying the Young-Laplace equation), contact angle continues to be satisfied because the small curvature of the wall at the pore throat allows that with very, very small movement of the actual contact point. The interface essentially is “stuck” at that pore throat, even though pressure from the outside is going up.
The interface is said to be “pinned” at the pore throat.
The upshot of this, for us, is that as you increase the pressure on the resin outside of your wood being impregnated, the amount of resin penetration is NOT continuous, or proportional to pressure, as you increase pressure. Rather (this is somewhat simplified), you can increase the pressure, and continue to increase the pressure, and those interfaces remain “pinned” at the pore throats, and you will NOT get any more resin into the wood.
(NOTE: I'm running into a limit on uploads - will need to split this posting and continue with a part 2....)
Last edited: